Servicing a Chronograph – We Followed Every Step
Chronograph Service
A few months ago, I visited a watchmaker and followed every step he did on servicing this vintage Valjoux 22 chronograph. Not only out of interest, but also to get an idea of all that work a watchmaker does to keep our watches ticking. As a showcase and to create a bit more awareness for this ancient profession. I ended up making an appointment with watchmaker Kalle Slaap.
Introducing the Watchmaker
Kalle Slaap runs a workshop in the picturesque village called ‘Grootschermer’, near Amsterdam. He also is watchmaking teacher at (nowadays) the only watchmaking school in The Netherlands, in Schoonhoven. His company is called ‘Horlogemaker Online’ (Watchmaker On-line). After years of working in the IT industry, Kalle decided to realize his dream: become a watchmaker. In the meanwhile, his company is an established name in The Netherlands. Together with his team, they focus on servicing and repairing vintage watches. Besides Kalle, about six other (apprentice) watchmakers work for his company.
There’s Always A Solution
As most of us know, finding parts is getting increasingly difficult. Sometimes parts are simply not available anymore. However, Kalle and his team do not stop at this point. They have a huge amount of original parts in stock and the professional machinery to re-create the missing parts if they aren’t available or reasonably priced (compared to the value of the watch). This is what I call future-proof watchmaking and repairing with an eye on the ever drying well of (vintage) watch parts.
Interesting Vision
As you probably know, I’m heavily focused on design matters. It was very interesting to hear Kalle speak about watches from a more technical point of view. It’s more about the inner workings of a watch that matters and motivates him.
Atelier Tour
Before we started with the actual watch service, I received a short tour around his atelier. His workshop is located in an old building with a rich history and served as a bank before it became Kalle’s atelier. To underline the focus on vintage watches, everything about the building is kept in its original condition (where possible). When you enter the workshop, it looks like you’re stepping into a place from back in the 1950s or 1960s. For example, check out his cabinets for storing watch parts. Of course, the surrounding changes when you enter the actual modern watchmaking room where everything looks organized and clean. Then, there is this third room where heavy machinery and tools are installed (for example, to polish watch cases and bracelets).
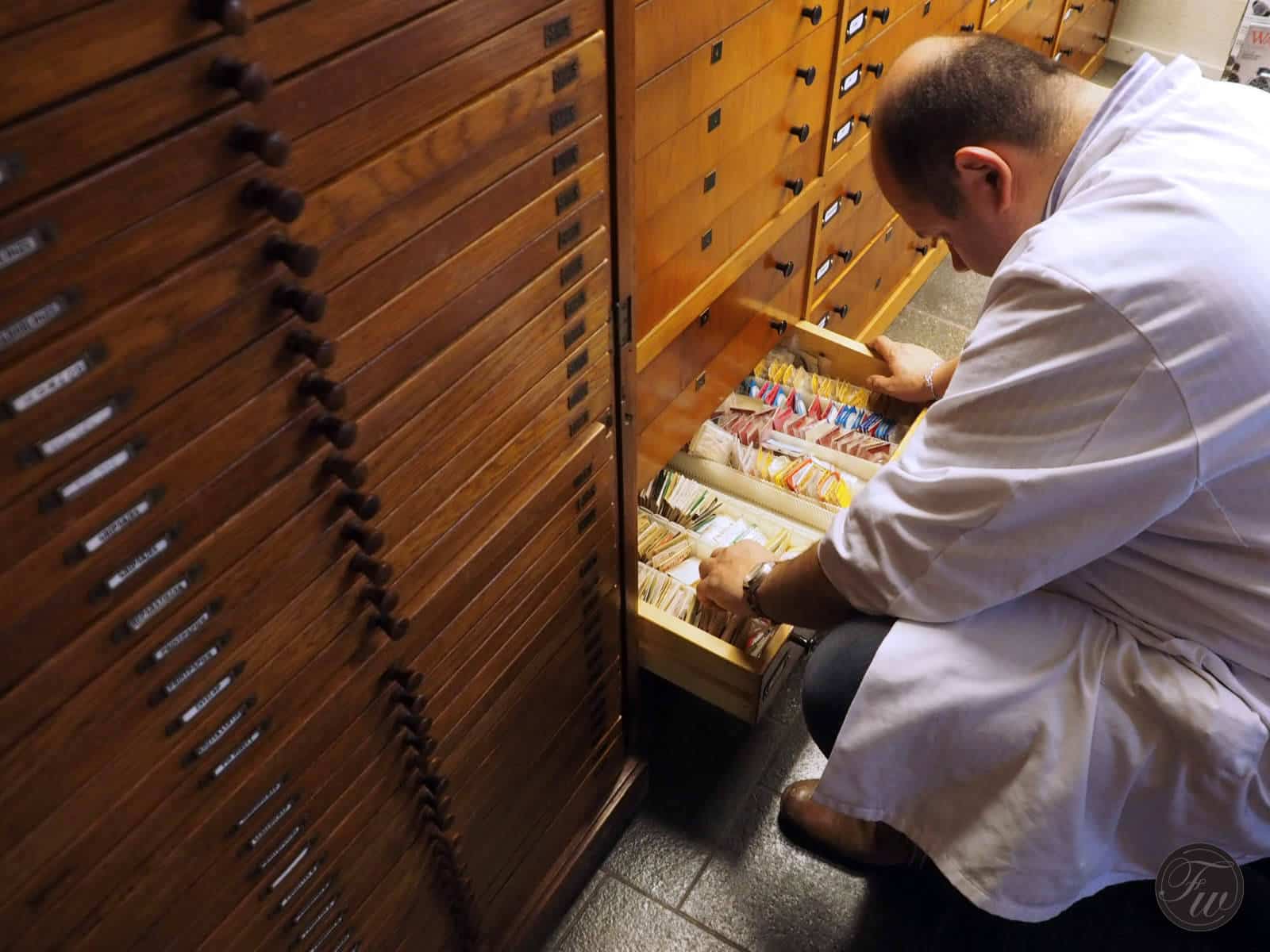
Vintage cabinets for stock
Chronograph Service: Eterna Telemeter with Valjoux 22
We looked at several candidates which were delivered for service and ended up with a 1940’s Eterna with telemeter scale for this showcase. We both thought this was the most interesting watch to show from a technical point of view. This particular service is mostly focused on the Valjoux 22 movement, but also some cosmetic optimizations later on. To keep things compact and interesting I’ve picked out the most remarkable and important parts during the watch service. The total service of this particular example was timed around 9 hours!
A service roughly consists out of the following stages:
- Intake: Conversation with client
- Visual Inspection outside
- Inspection inside
- Monitoring
- Disasembling and grouping parts
- Cleaning process
- Assemble and install parts
- Testing
- Finishing process
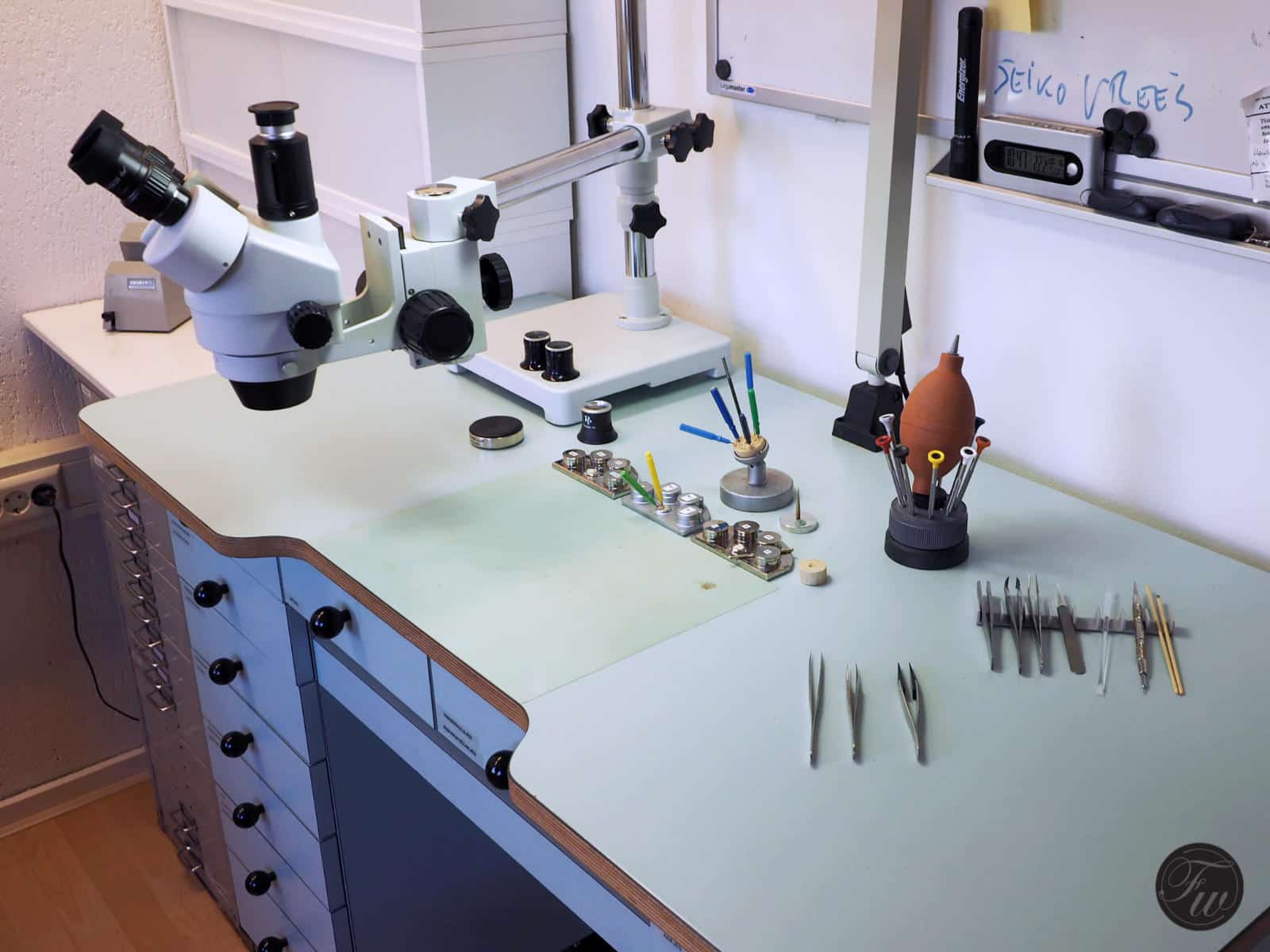
The ‘desk’ of a watchmaker
1. Intake: Conversation with Client
As with most watches that appeared on his to-do list, this Eterna also came in without any hints as to the problem. It’s always a (small) journey for the watchmaker to identify the problem with descriptions like “the watch isn’t running anymore; can you fix it?”. Most of the time the problem will show up during a full service, as it was the case with this one.
2. Visual Inspection
Then the thorough inspection starts. Kalle starts with the outside. Are all parts in good shape and do all the chronograph functions work properly? Then, the disassembling takes place. In this case the bezel with crystal is being removed by a special spring loaded tool.
3. Inspection inside
After this is done, the snap-on case back is removed. Inside, a highly appreciated Valjoux 22 manual-wound column-wheel chronograph with 17 jewels, 40 hours of power reserve and a frequency of 18000 A/h. If everything looks ok, it’s time to wind it and check its ‘heartbeat’.
4. Monitoring
Kalle puts it on the timegrapher to measure the ‘heartbeat’ of the watch when it runs. A watchmaker can conclude a lot based on the graphs from this machine. Just like a doctor who listens to someones heart with a stethoscope. Besides accuracy, the amplitude of the balance is a very important indicator as is the beat error value.When this is done, Kalle moves on to further dissasembling.
5. Disassembling and Grouping Parts
After removing the screws which fix the movement on the case Kalle turns the watch and removes the hands.
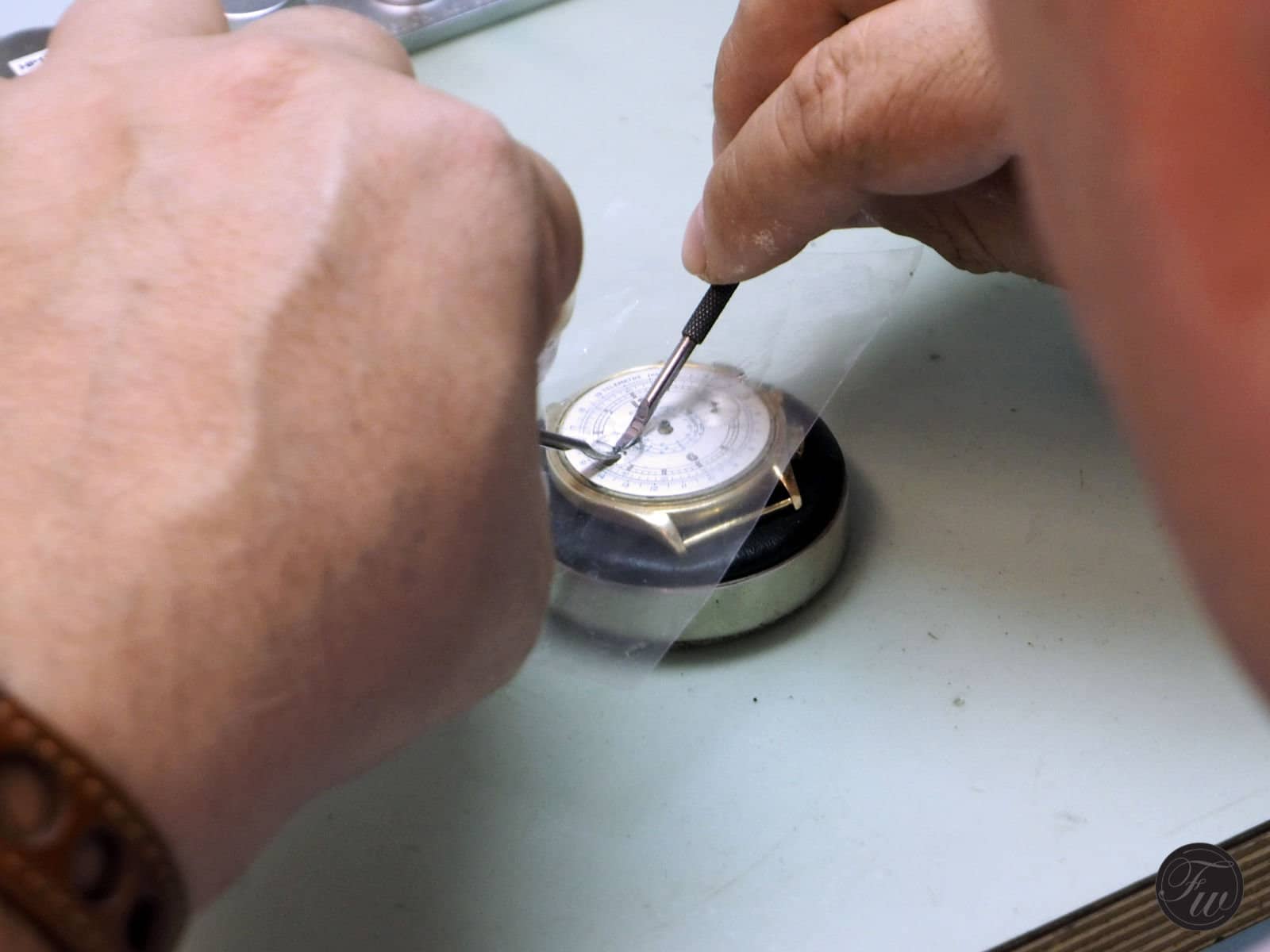
Removing the hands
Every part is removed in a strictly ordered pattern in a modular way. By doing this the watchmaker can keep track of all parts and it makes detecting problems and assembling a lot easier.
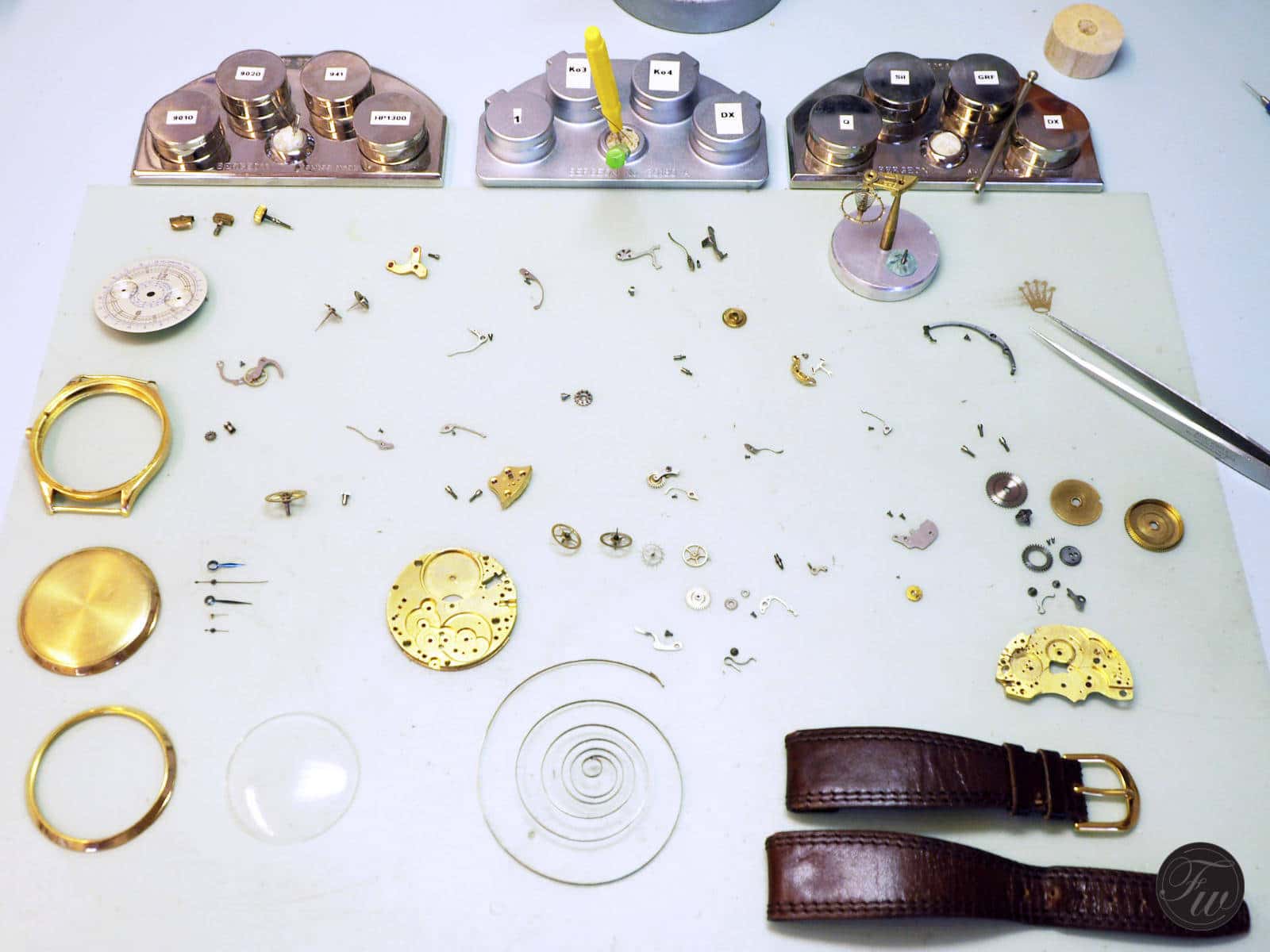
Overview of the disassembled watch
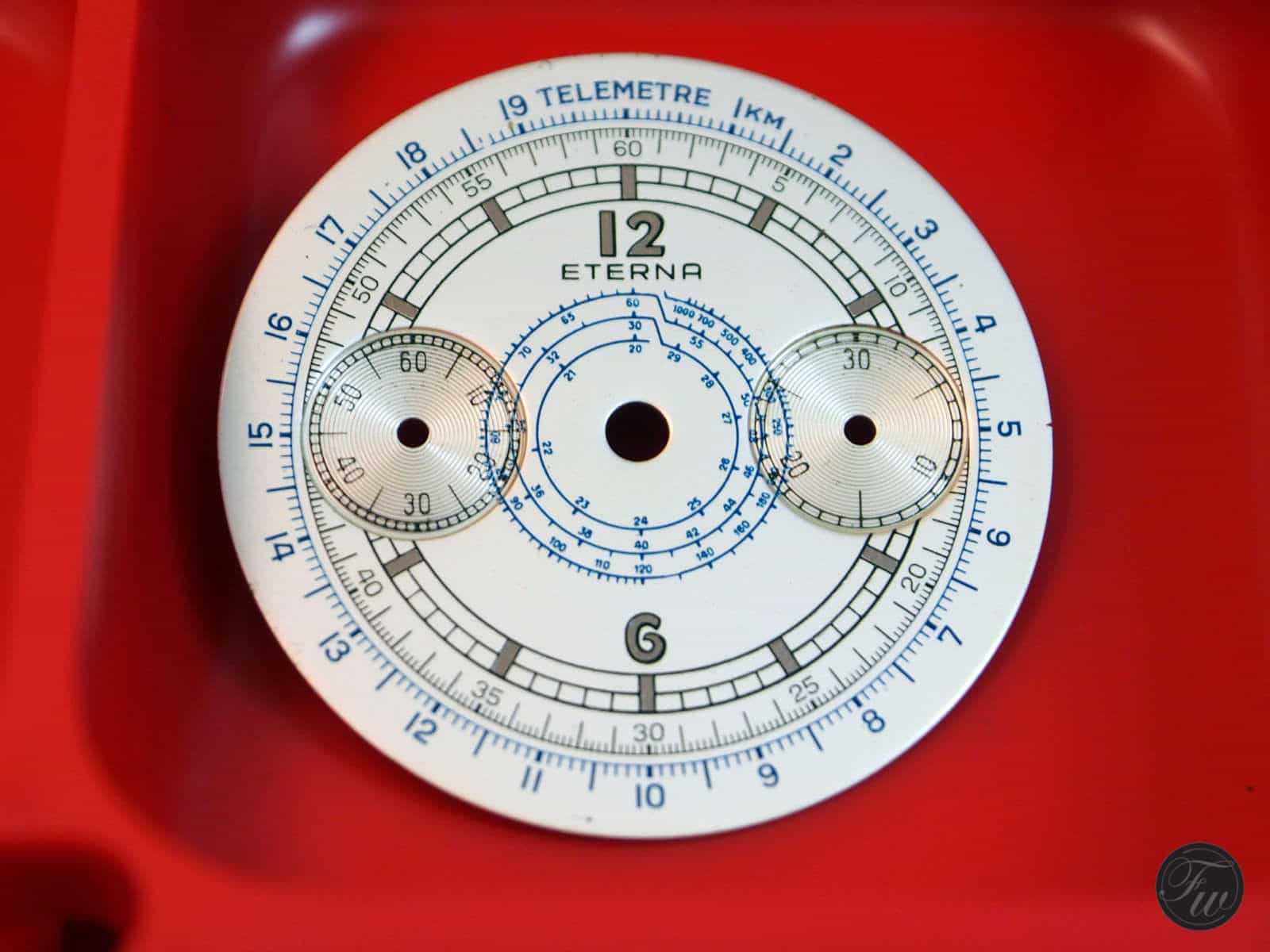
Dial is in fantastic condition
To the remove some parts special tools are used. For example, this Presto tool to remove uneven spoked wheels:
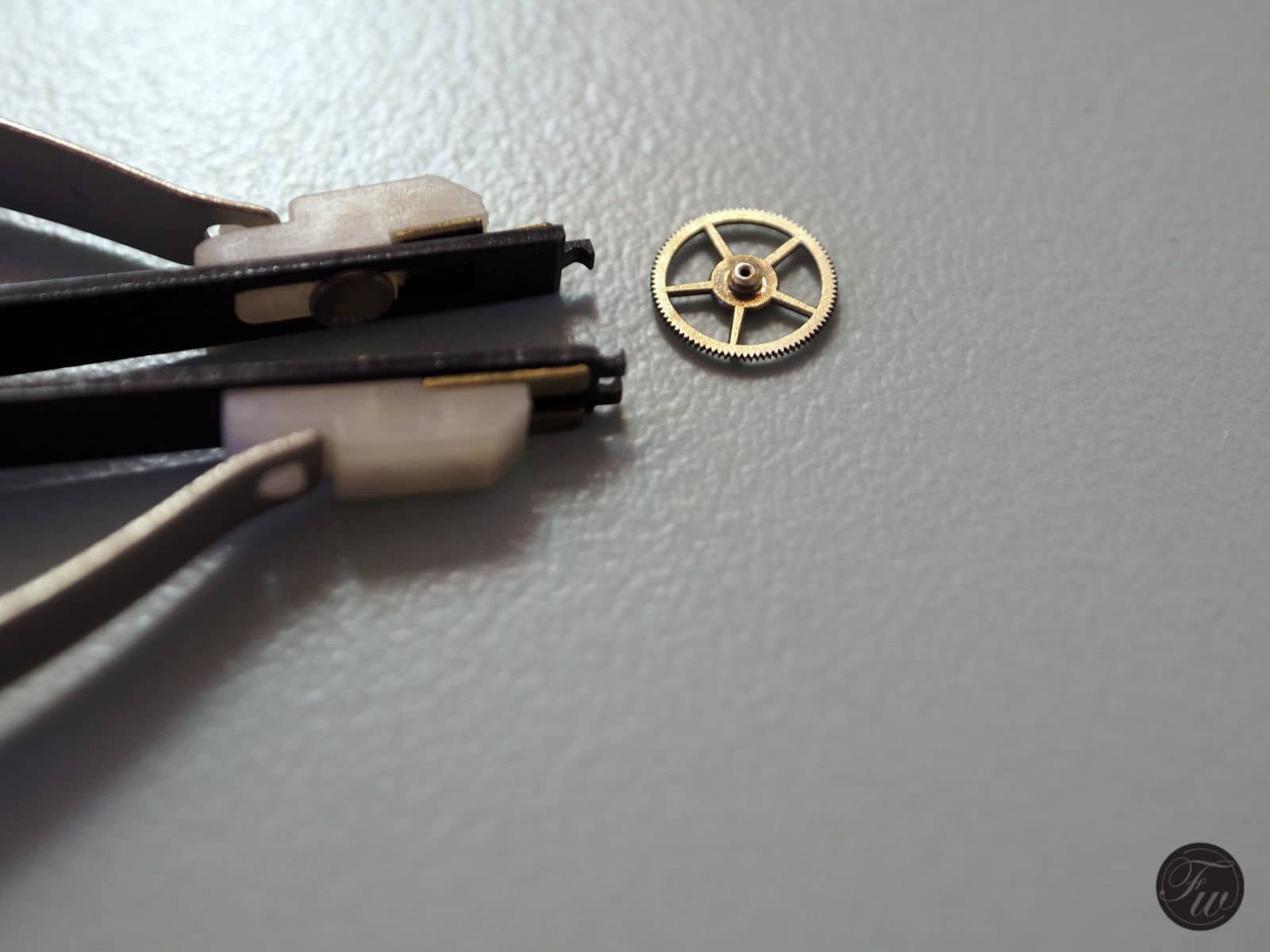
Presto tool
Some fragile and vital parts get a special treatment. The balance-wheel with its bridge plate and spring is placed on a watch balance tack tool to secure the balance spring and staff.
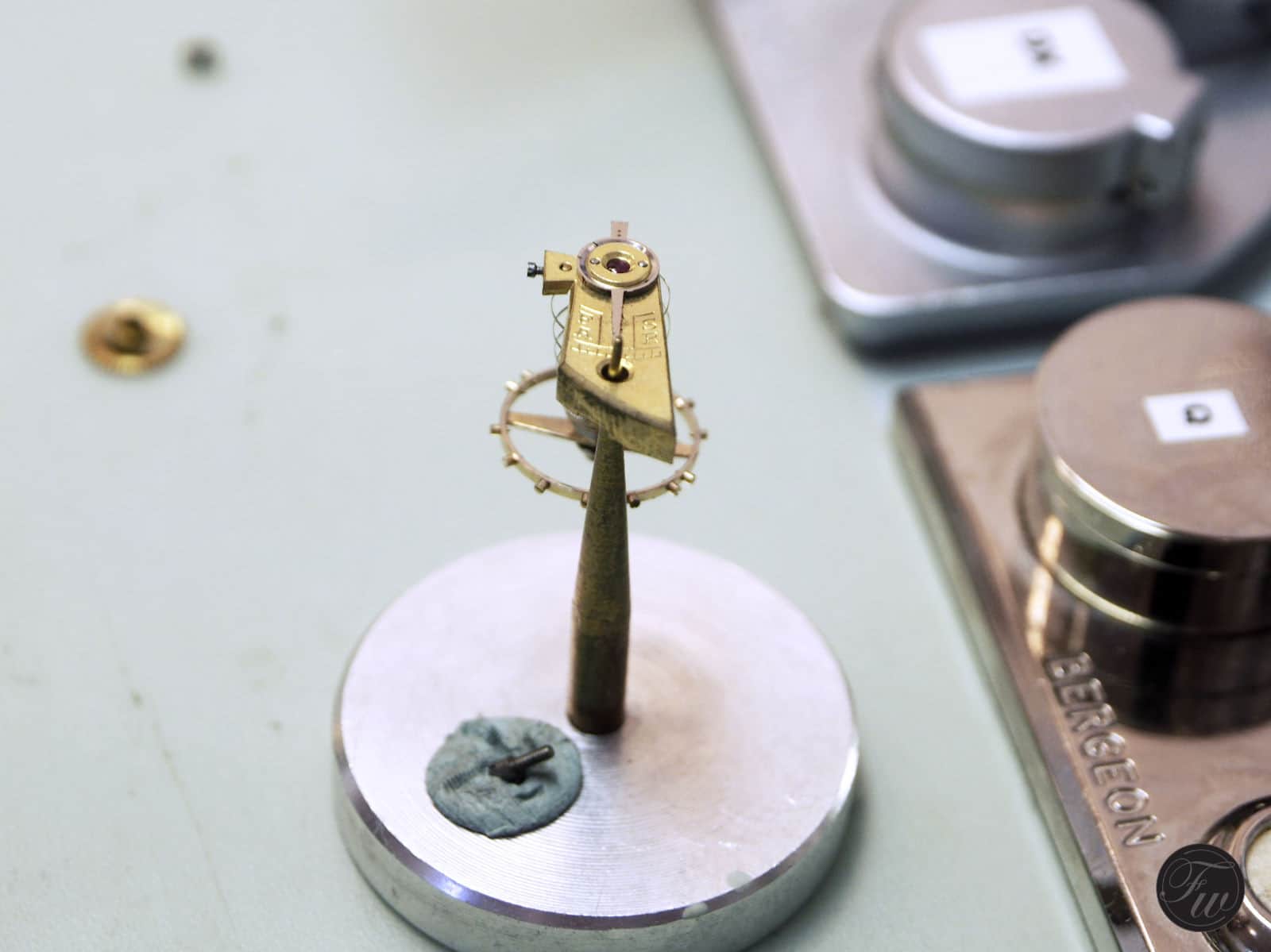
Balance tack tool
After grouping every group is distributed in small baskets. Kalle puts the basket in a cleaning machine for a thorough cleaning session.
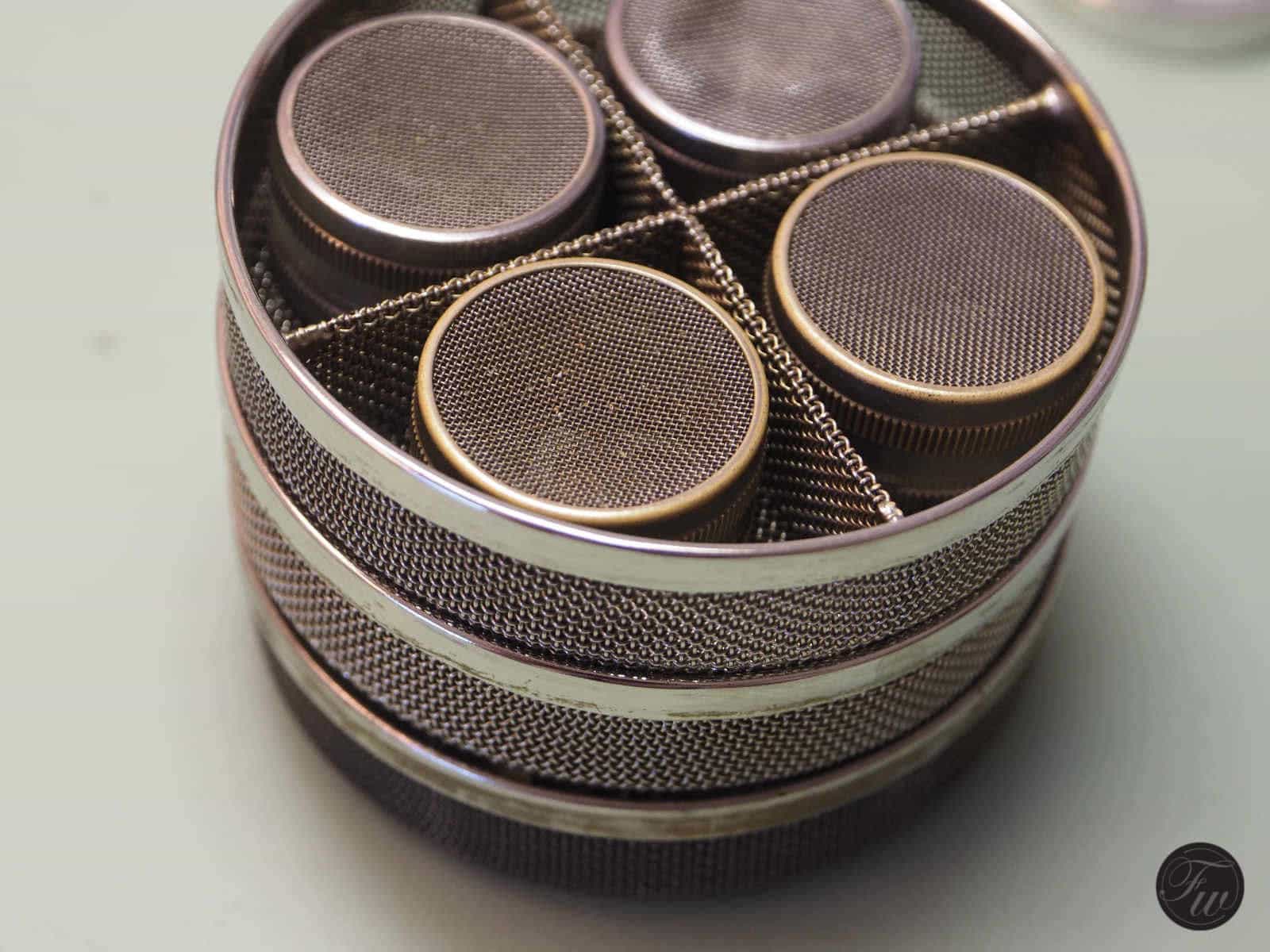
Cleaning basket with smaller baskets for part groups
6. Cleaning Process
All disassembled parts are placed in the cleaning machine at the same time. This process could be split up in 4 anhydrous baths
- 2 cleaning solution
- 2 rinse fluid
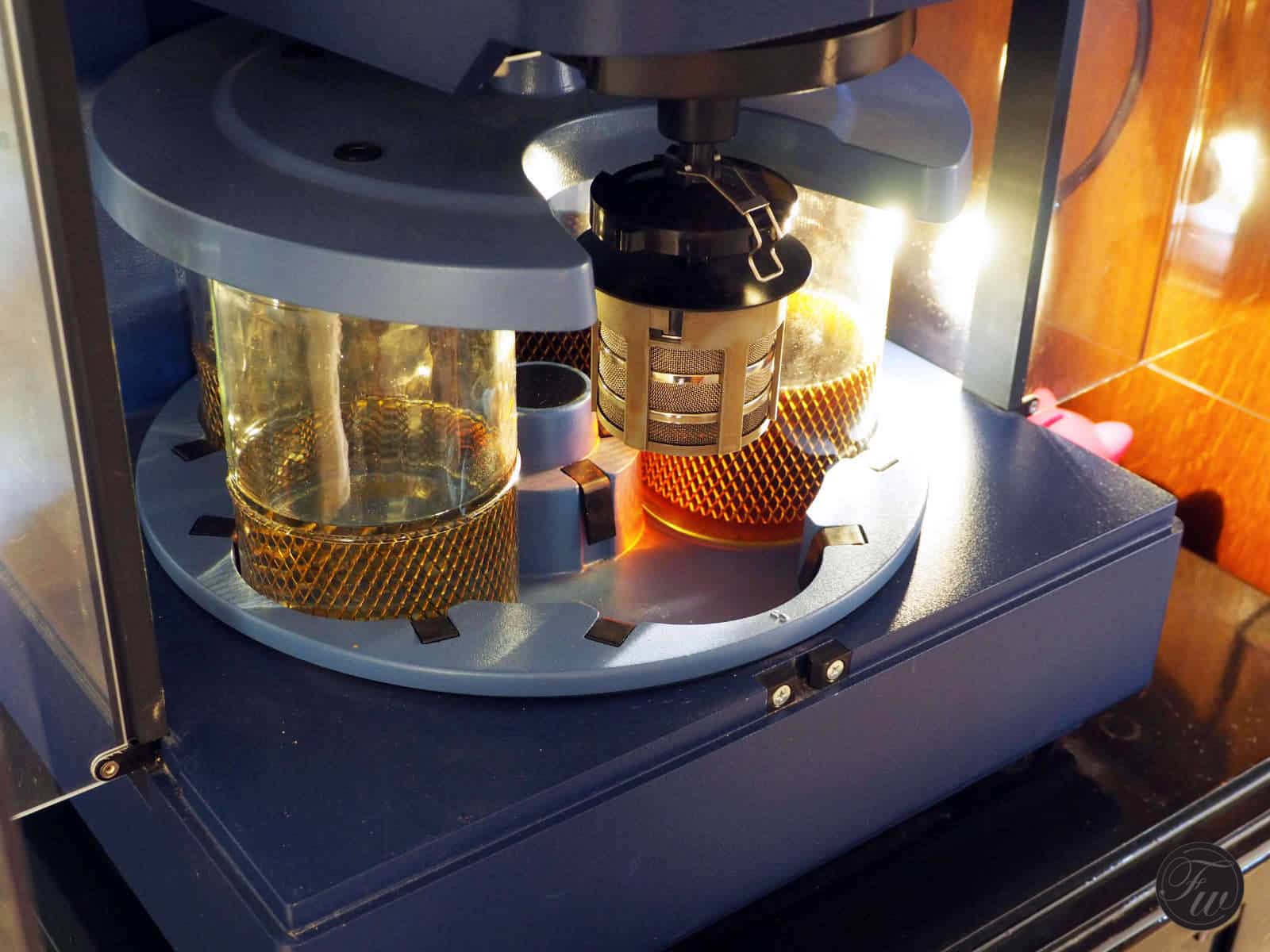
Cleaning machine with 4 baths
After this cleaning process, the machine dries all the parts. Kalle inspects every part individually after this process. The inspection is done comprehensive and carefully.
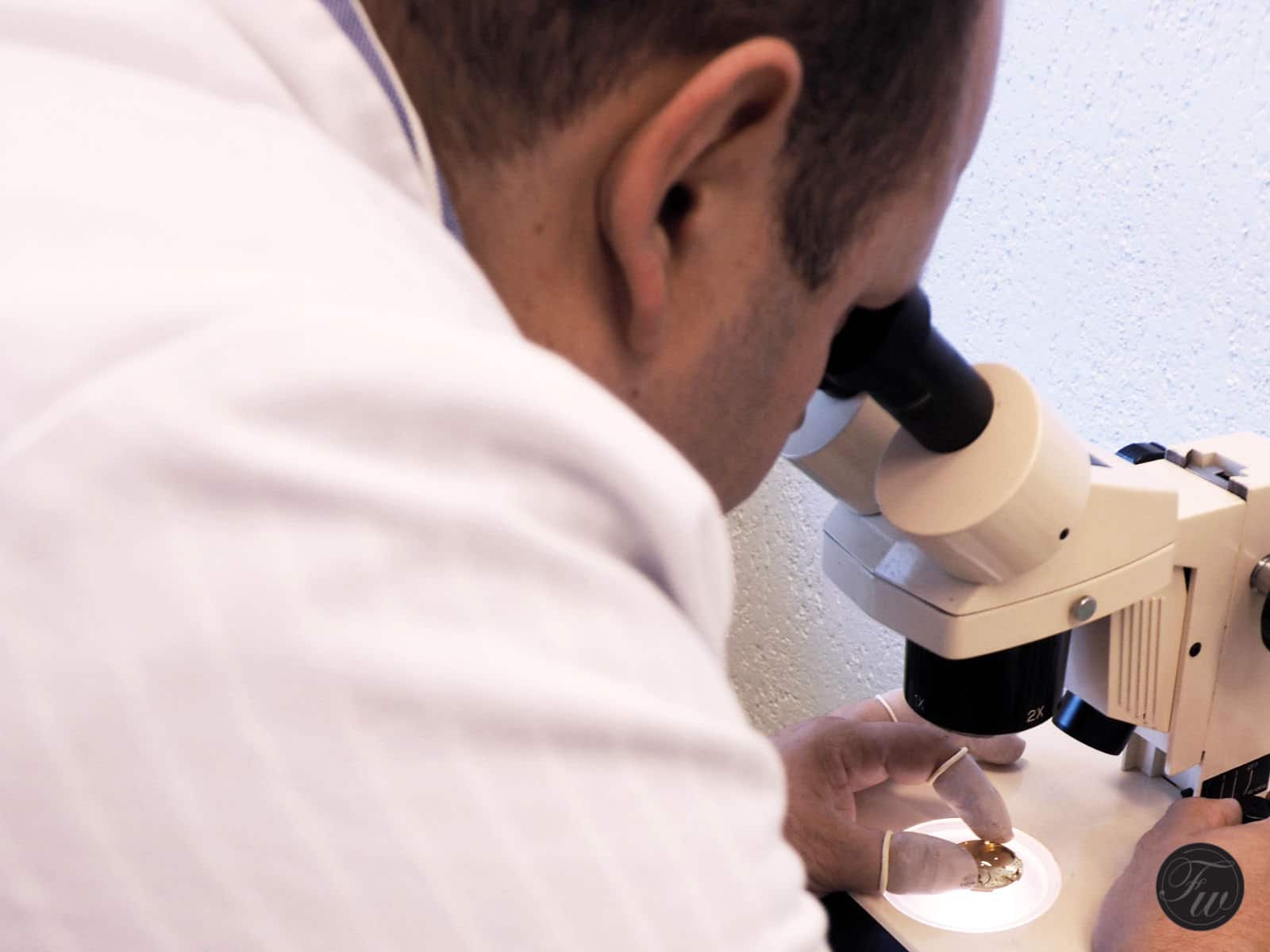
Comprehensive inspection
The case parts, like the case back, get their own ultrasonic bath. This specific water based bath is being warmed and specifically meant to clean the dirt/skin oils of parts with the help of ultrasonic vibration.
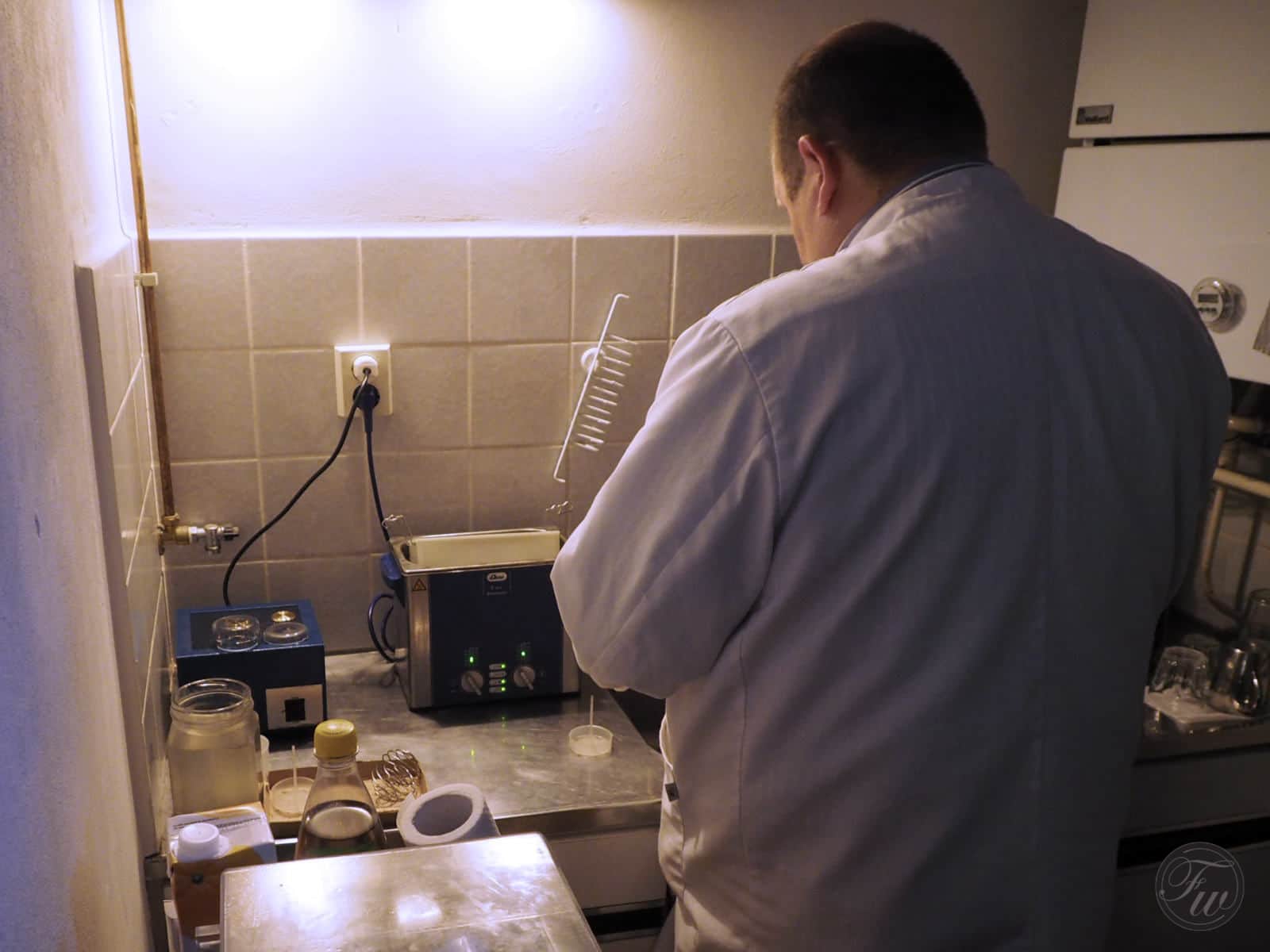
The Ultrasonic bath (silver machine next to Kalle)
7. Assemble and Install Parts
After the inspection the long process of assembling take place, if no errors are identified or broken parts have been found. In that case, they need to be fixed or replaced.
Kalle puts different plates and bridges under the backlit microscope to see if there are any broken jewels that need to be replaced. As most of us know, these are vital parts to handle friction. It turns out that there were several broken ones. After getting the right sizes with a micrometer Kalle picks out the right ones from his stock and places them with a so called jewelling tool.
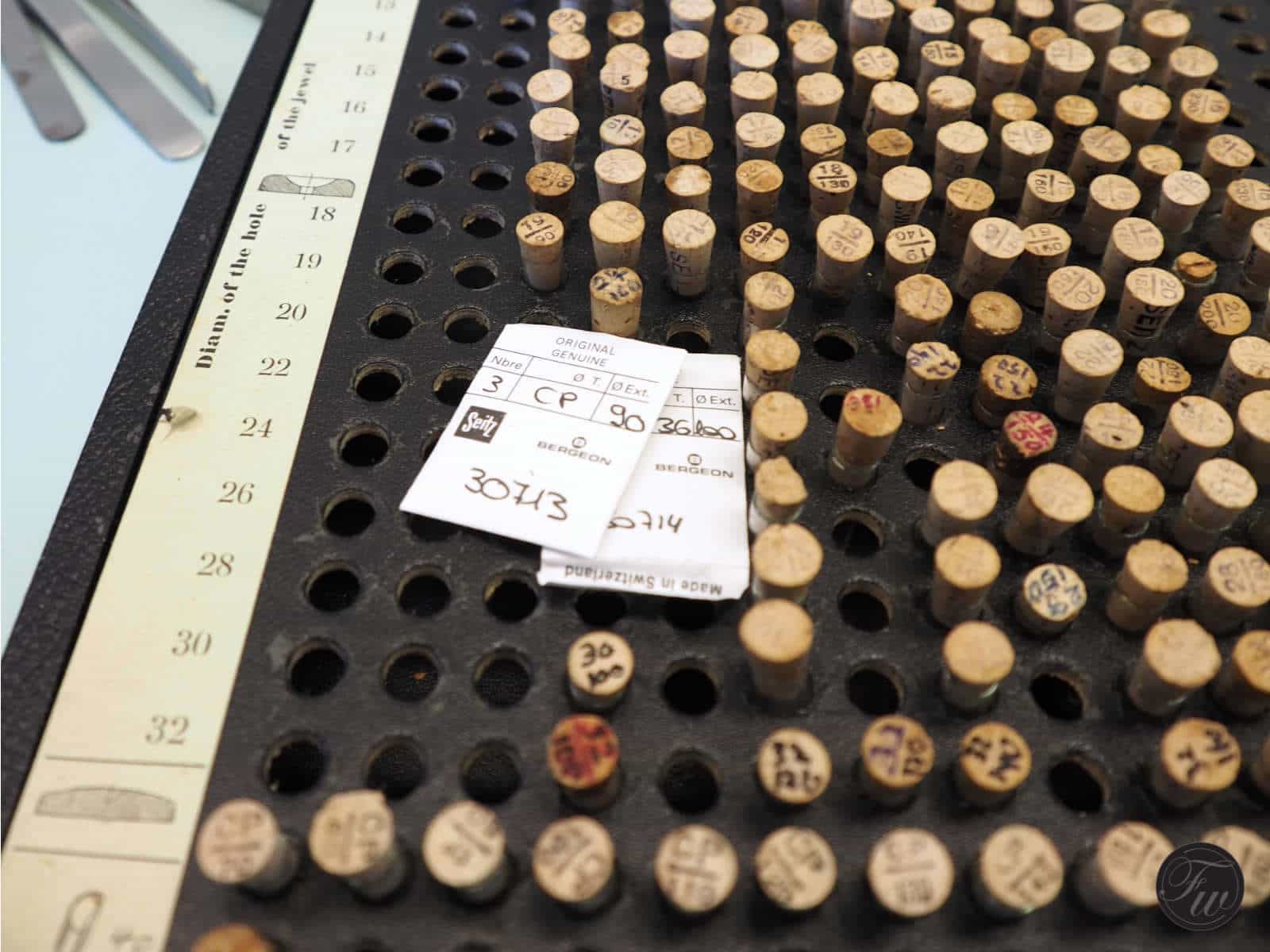
Jewel stock
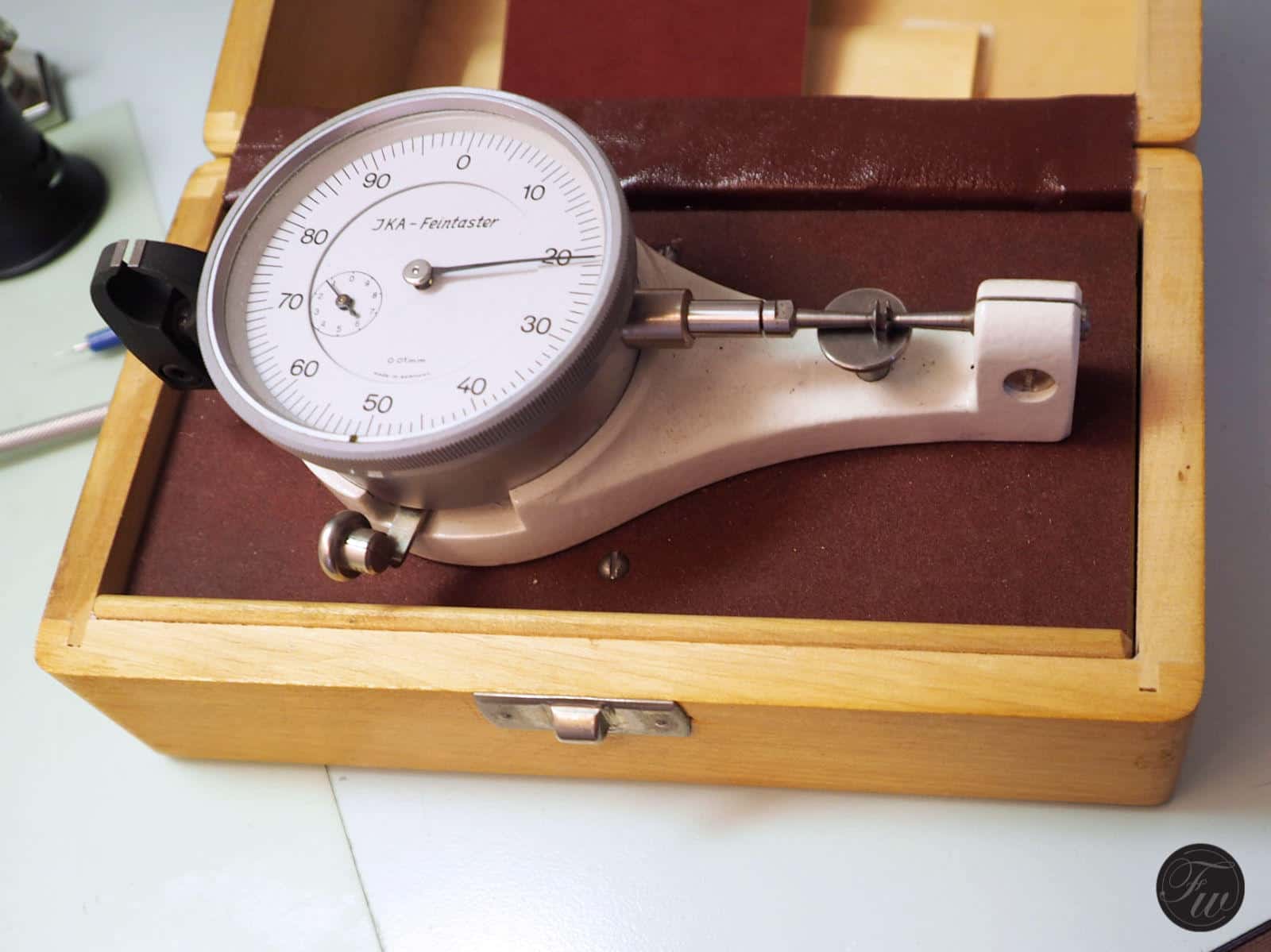
A micrometer to measure jewels
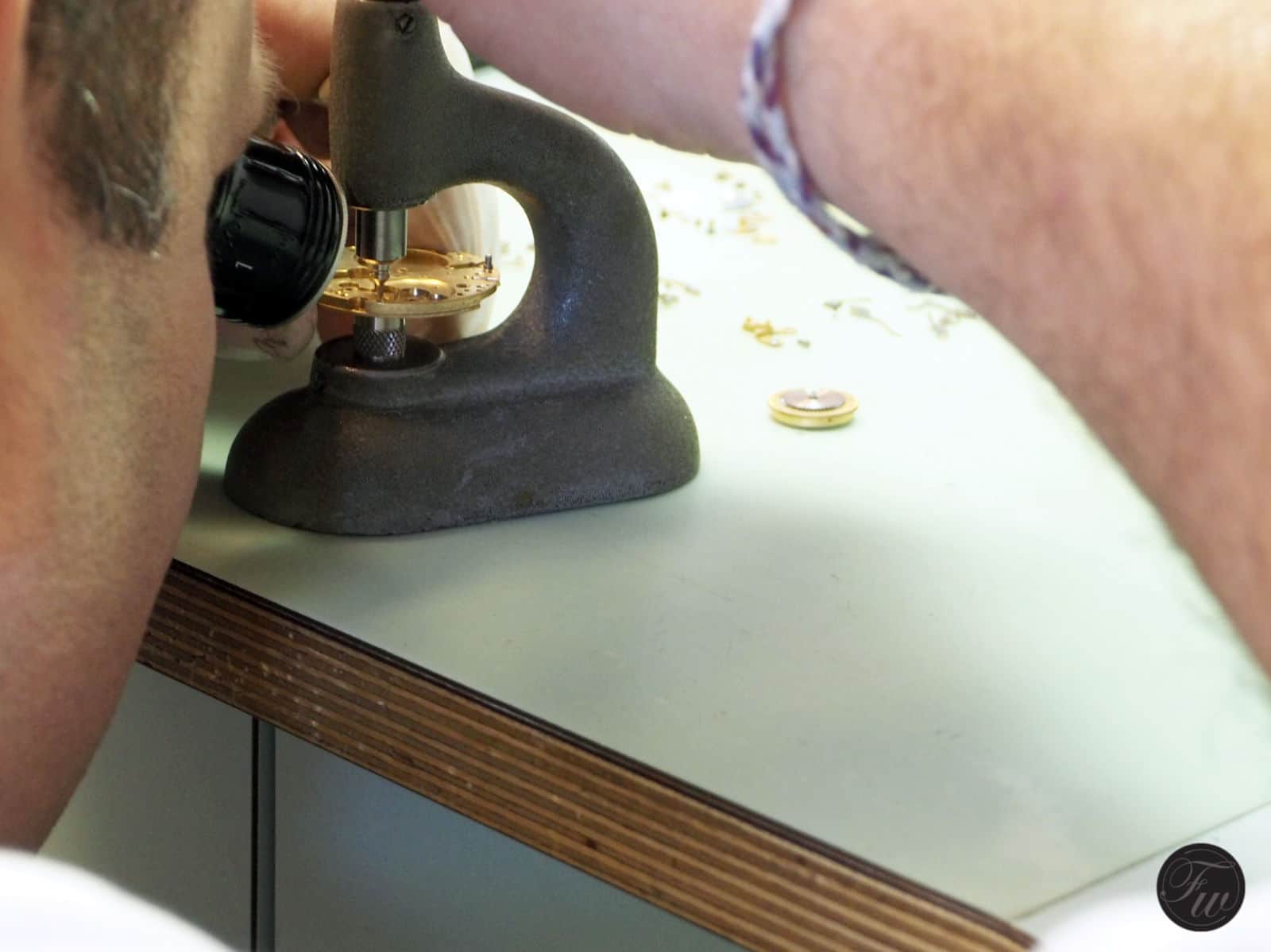
Kalle presses the jewels in the designated holes
The assembly is being done with different tweezers and sharpened screwdrivers. Sometimes even more than one tool is required to install different parts. For example, in the image below, a dip watch oiler is being used to fix the click (for the ratchet wheel) while screwing the mainspring barrel bridge.
Next is the assembly of the mainspring barrel, the power source of the movement. The mainspring is sandwiched by a closed (and oiled) cover and the barrel. The cover is assembled by pressing it on the barrel.
Checking proper functioning of the escapement by manually putting the pallet fork in the right or left position:
After this the balance bridge with balance-wheel and balance spring is assembled:
The winding stem is being adjusted and deburred:
8. Testing
All essential parts (winding mechanism, mainspring, gear-train and escapement) need to be assembled to get the watch up and running. Next is a check if it has a healthy amplitude and beat rate.
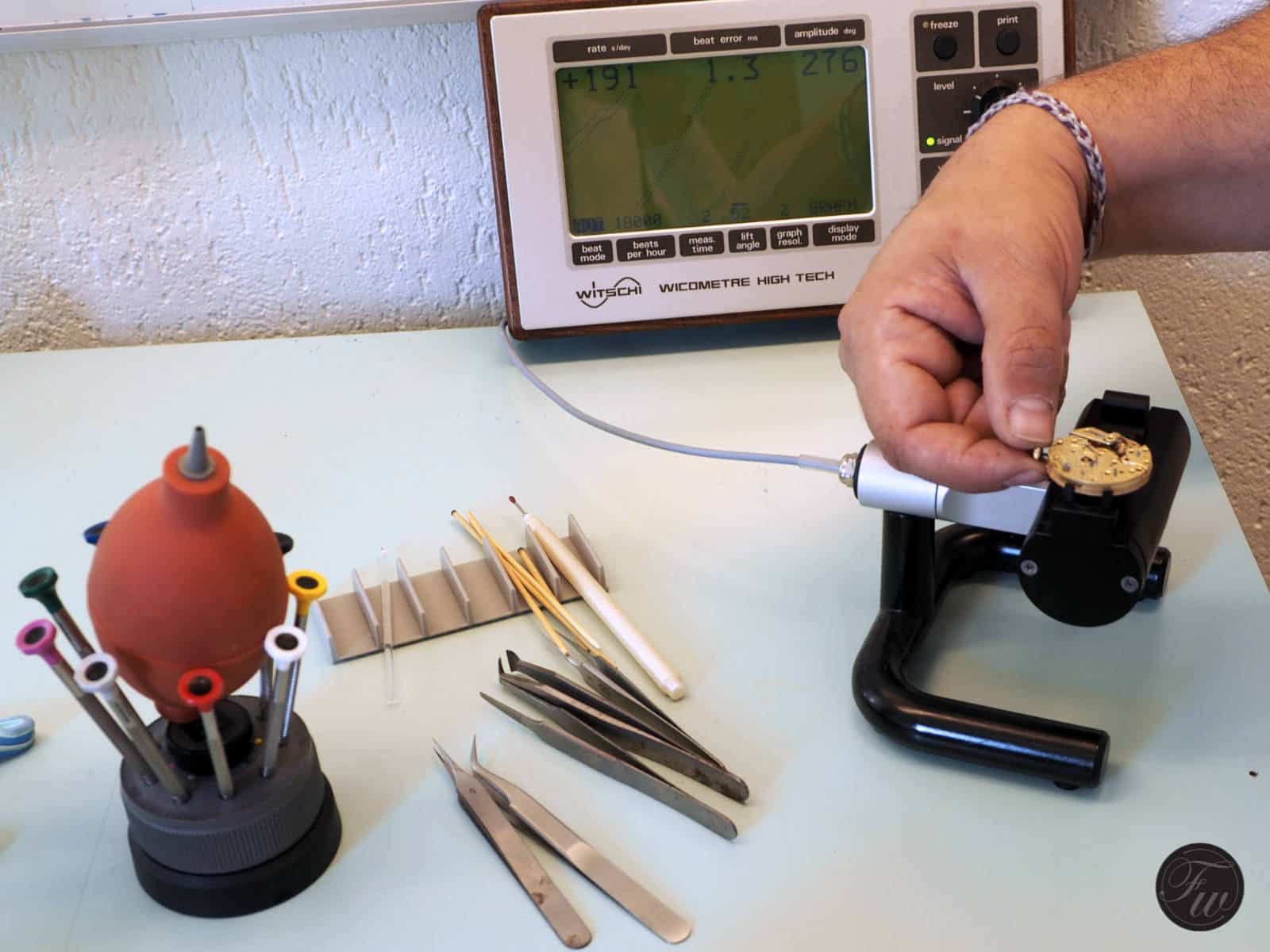
Measuring the ‘heart beat’
In this case there were errors… After an inspection under the microscope it turned out that the balance spring was deformed causing unacceptable beat error value. So unfortunately, no ‘finish line’ yet.
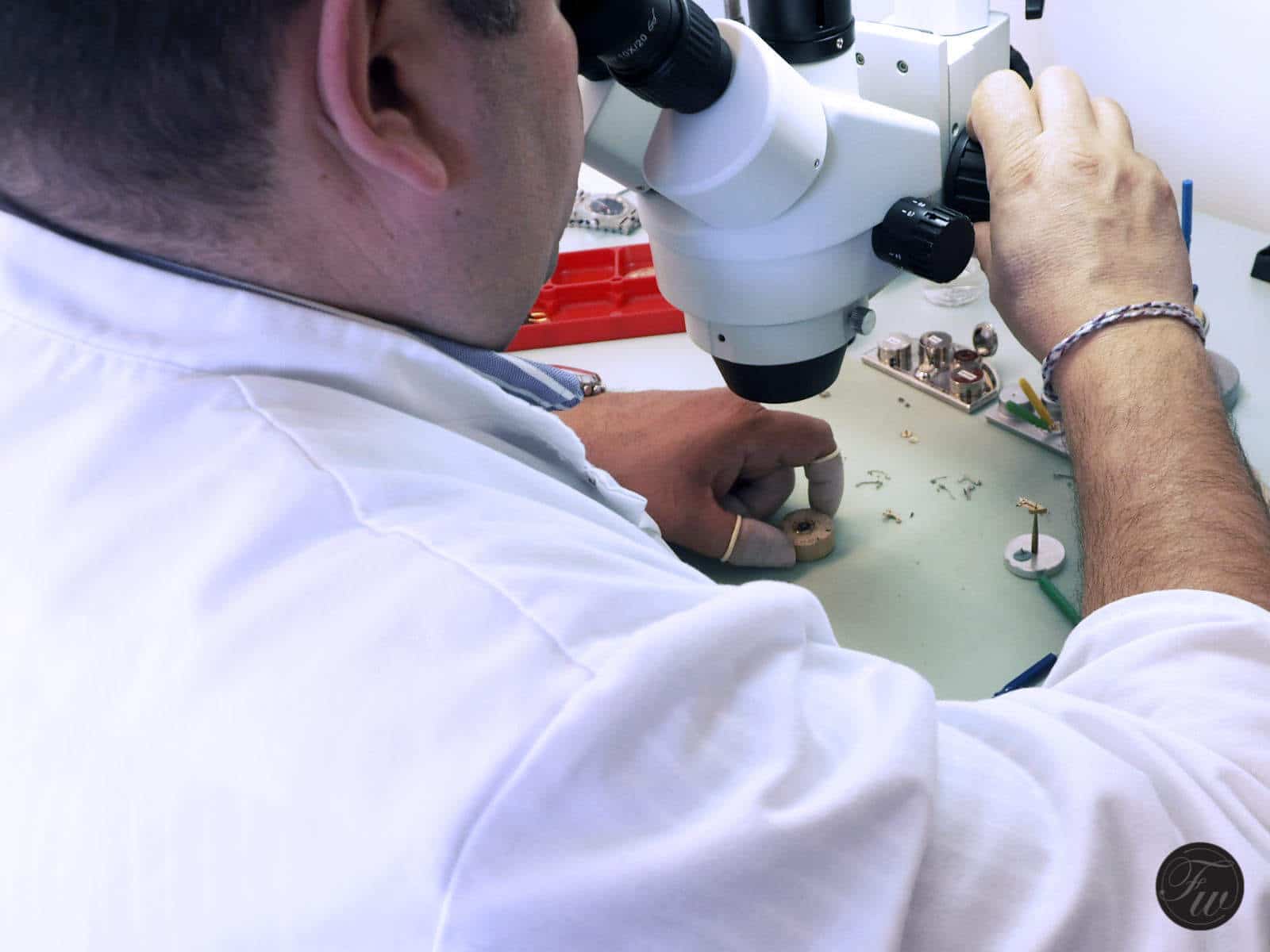
Inspection of the balance wheel under the microscope
The problem was solved by manually adjusting and bending the spring back to its initial shape. Delicate work for a true craftsman. After seemingly endless inspection and testing Kalle moved on to the ‘next step’.
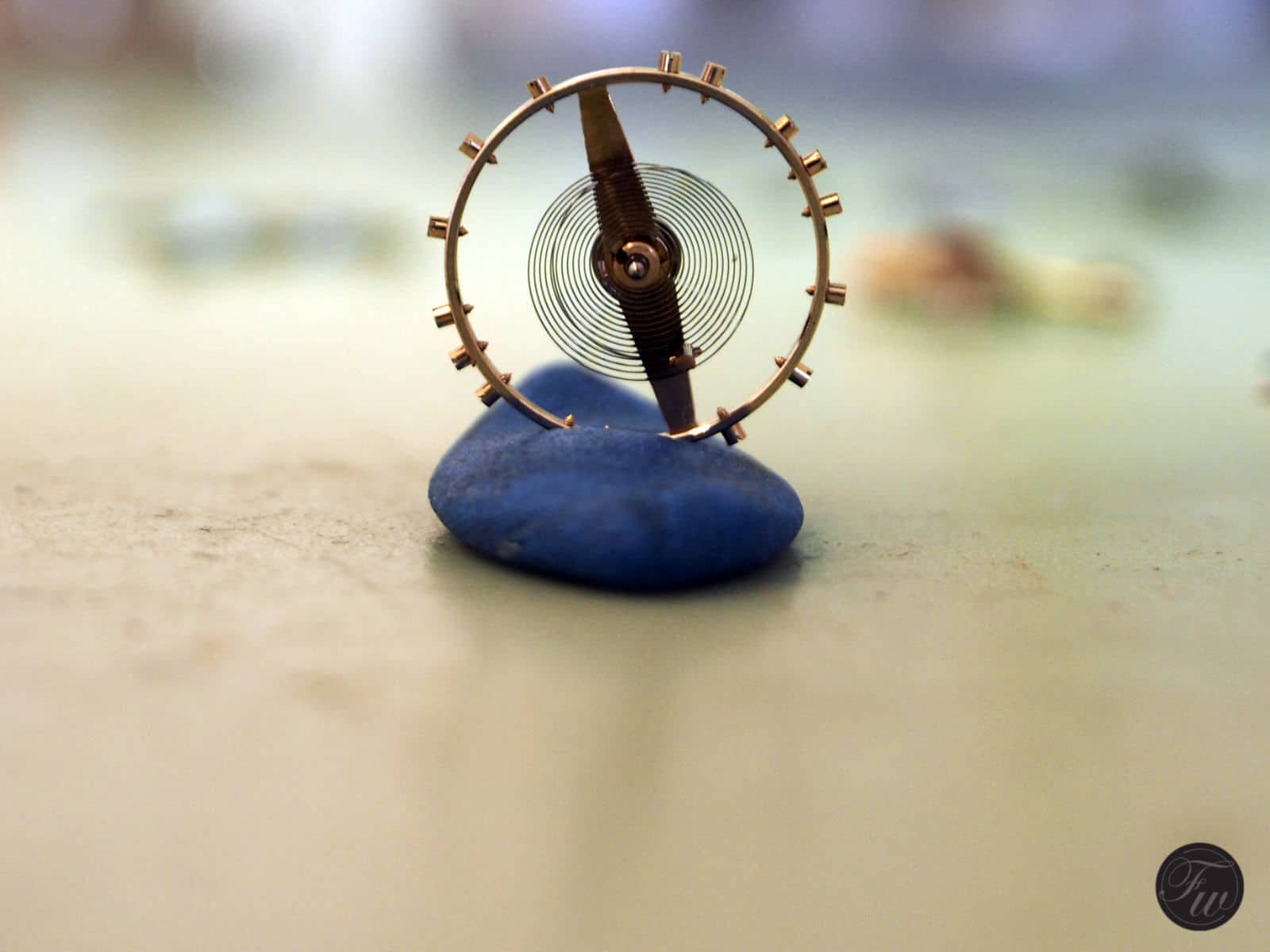
The part which was causing the error: the balance spring
Kalle made a nice movie to show the functioning of the spring in slow motion:
With a satisfactory functioning of the movement, the specific chronograph parts need to be checked as well. Some parts definitely need oiling, others need grease. For example, a staff on the chronograph:
Assembling the heart of the chronograph functions: the column-wheel. Kalle checks if it functions properly by manually trigger rotations with the connected cams.
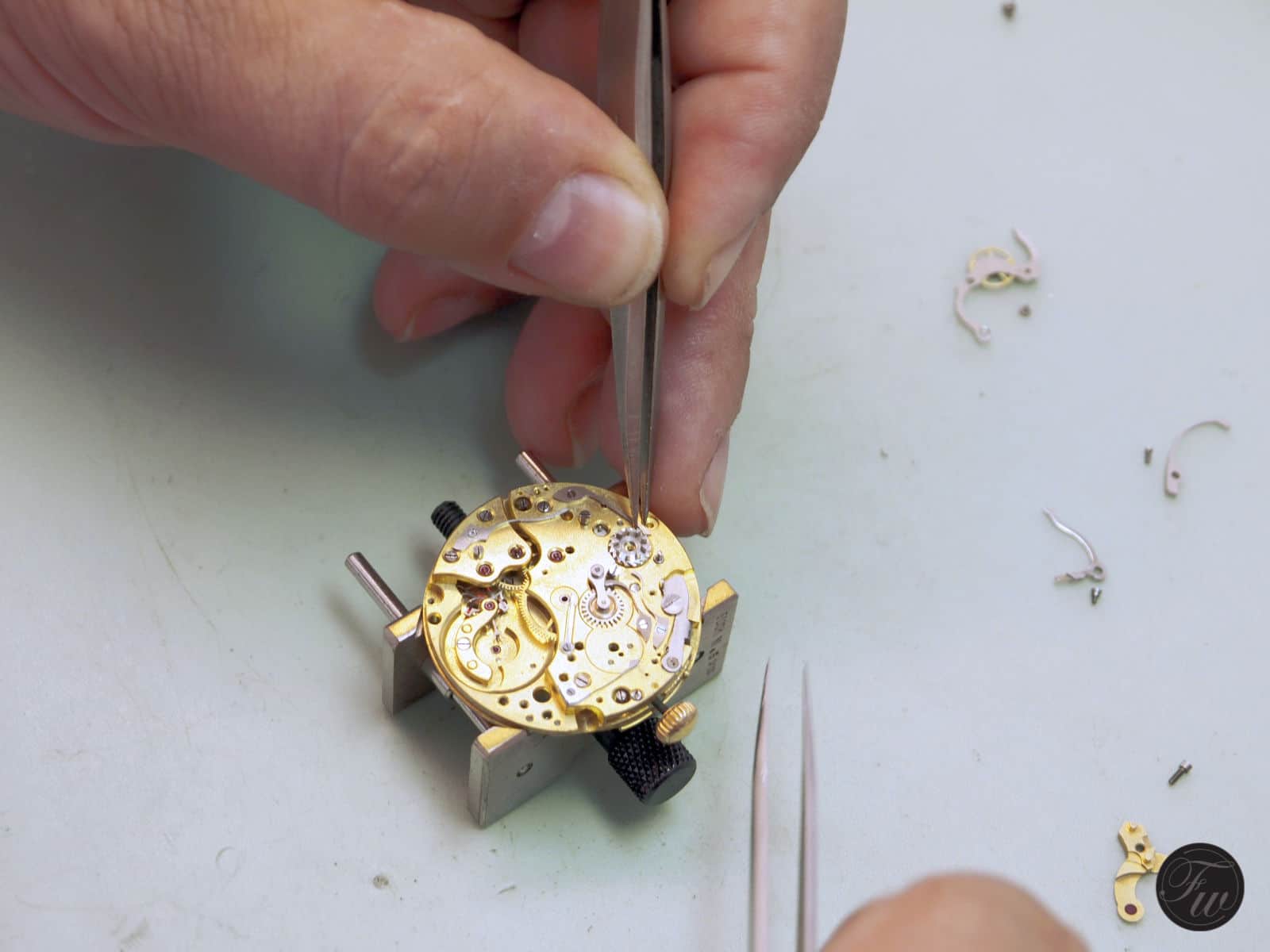
Check if the column wheel functions properly
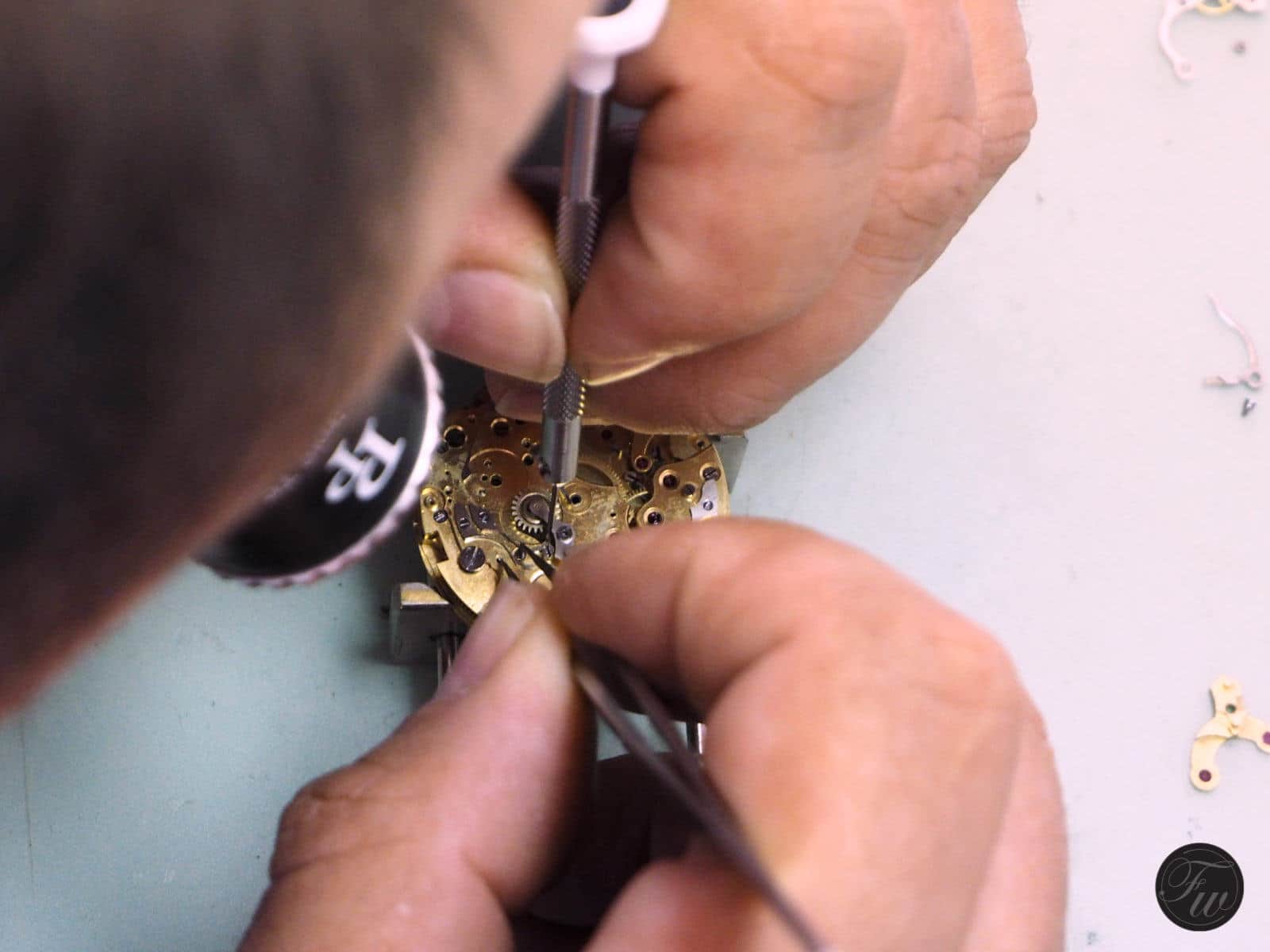
Installing chronograph parts
9. Finishing Process
The service of the chronograph is almost finished. After the assembly of the chronograph movement and passing all the tests, Kalle turns the watch over in order to install the dial and hands.
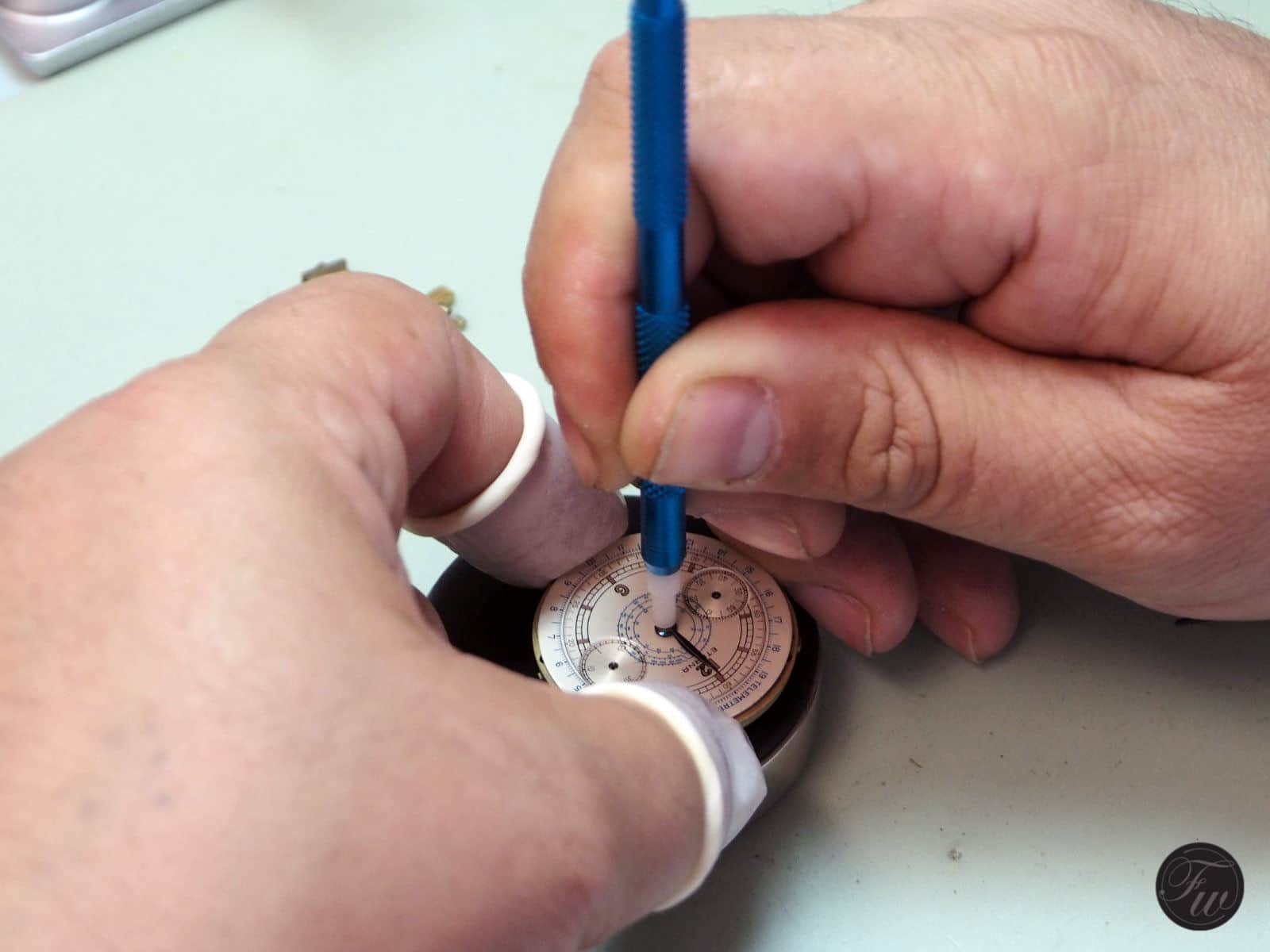
Pressing of the hands
Even though the case wasn’t in a very bad condition, Kalle decided to give it a light polish. With a polishing machine he redefines the radial finish on the case back and remove small scratches from other parts without taking too much material and without ruining the original shape of the case.
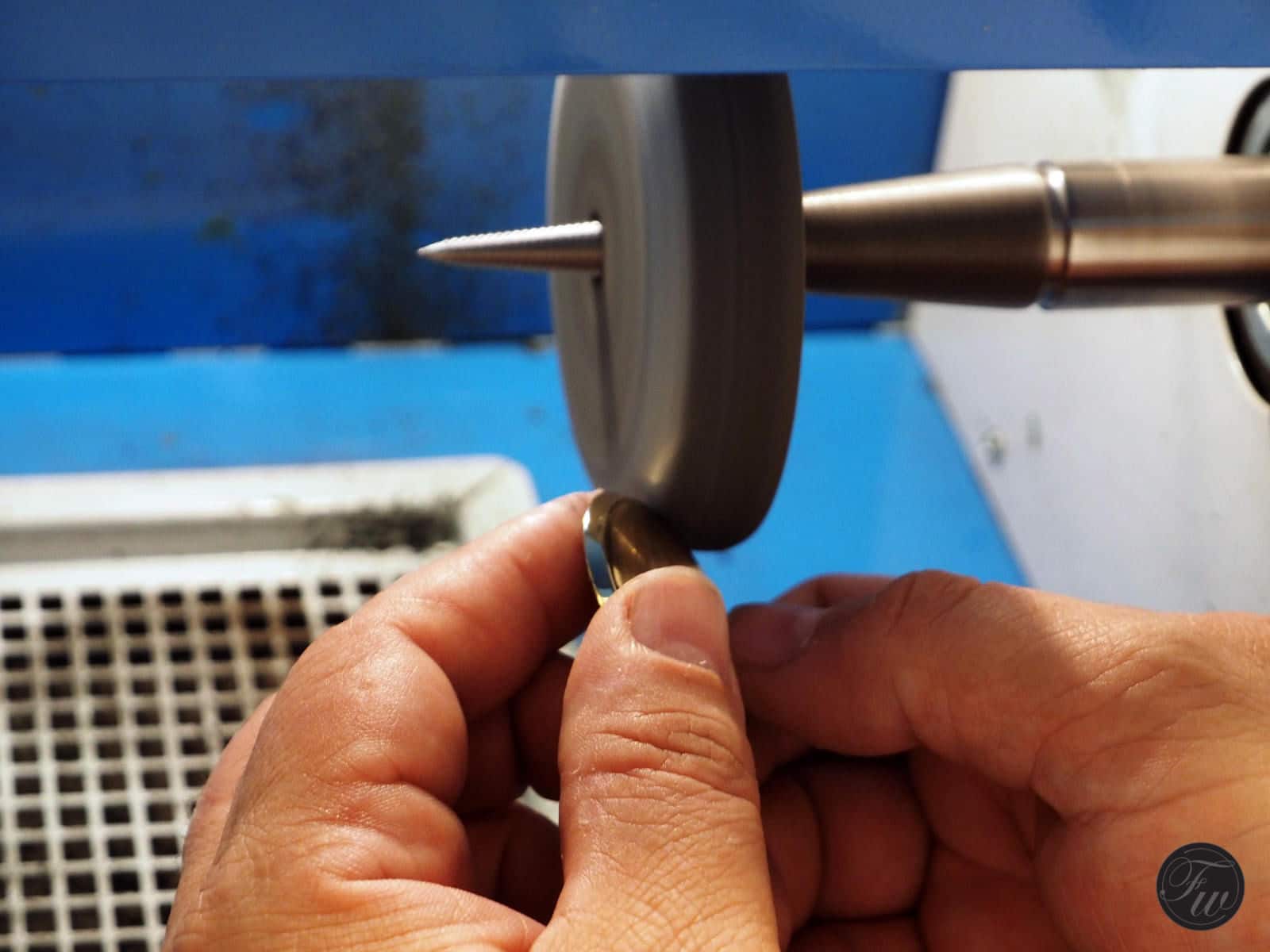
Gentle case polishing
Kalle cases the movement and fixes it into position using the screws. After lubrication, he assembles the pushers and winding stem.
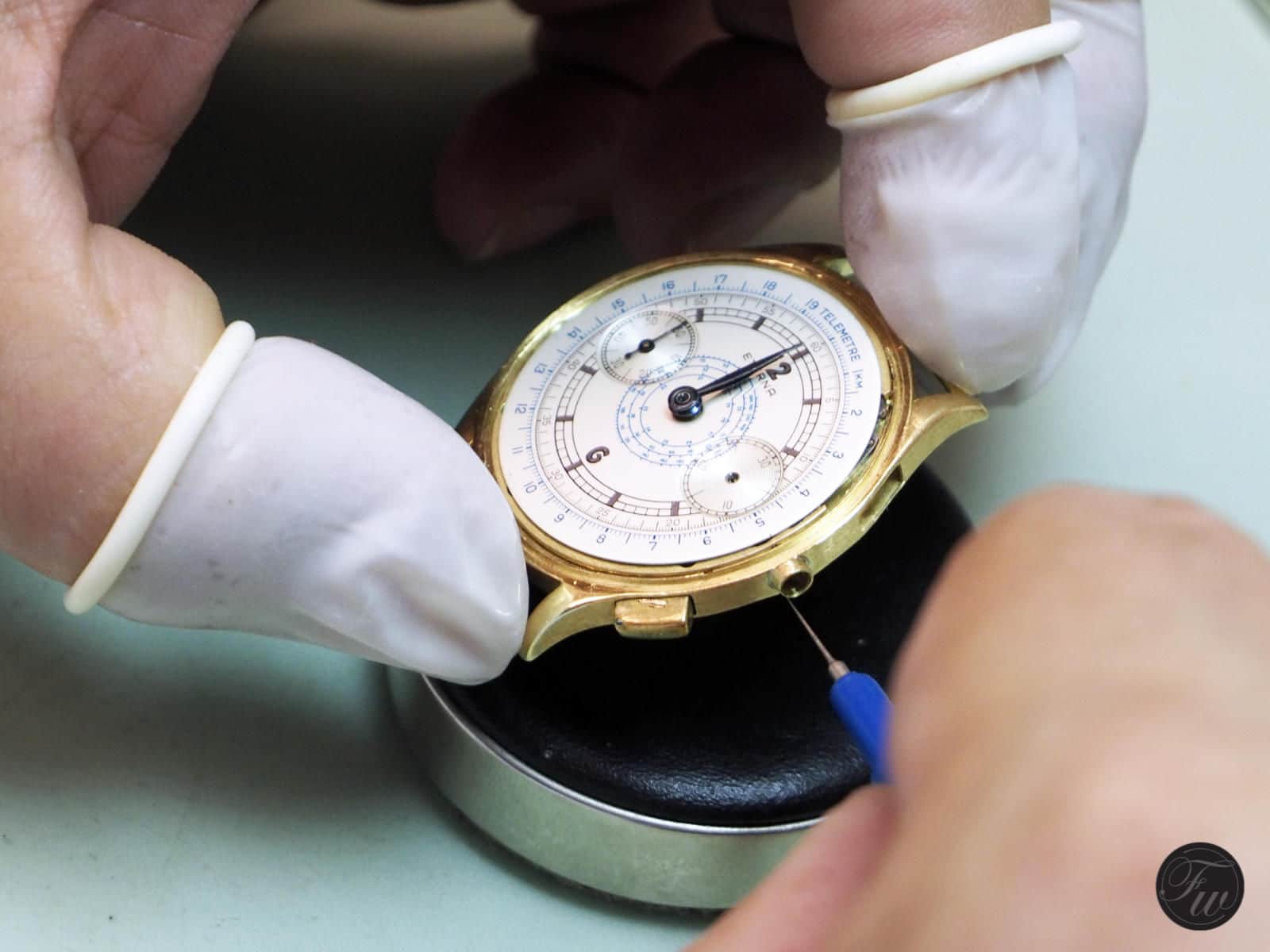
Lubrication for the winding stem
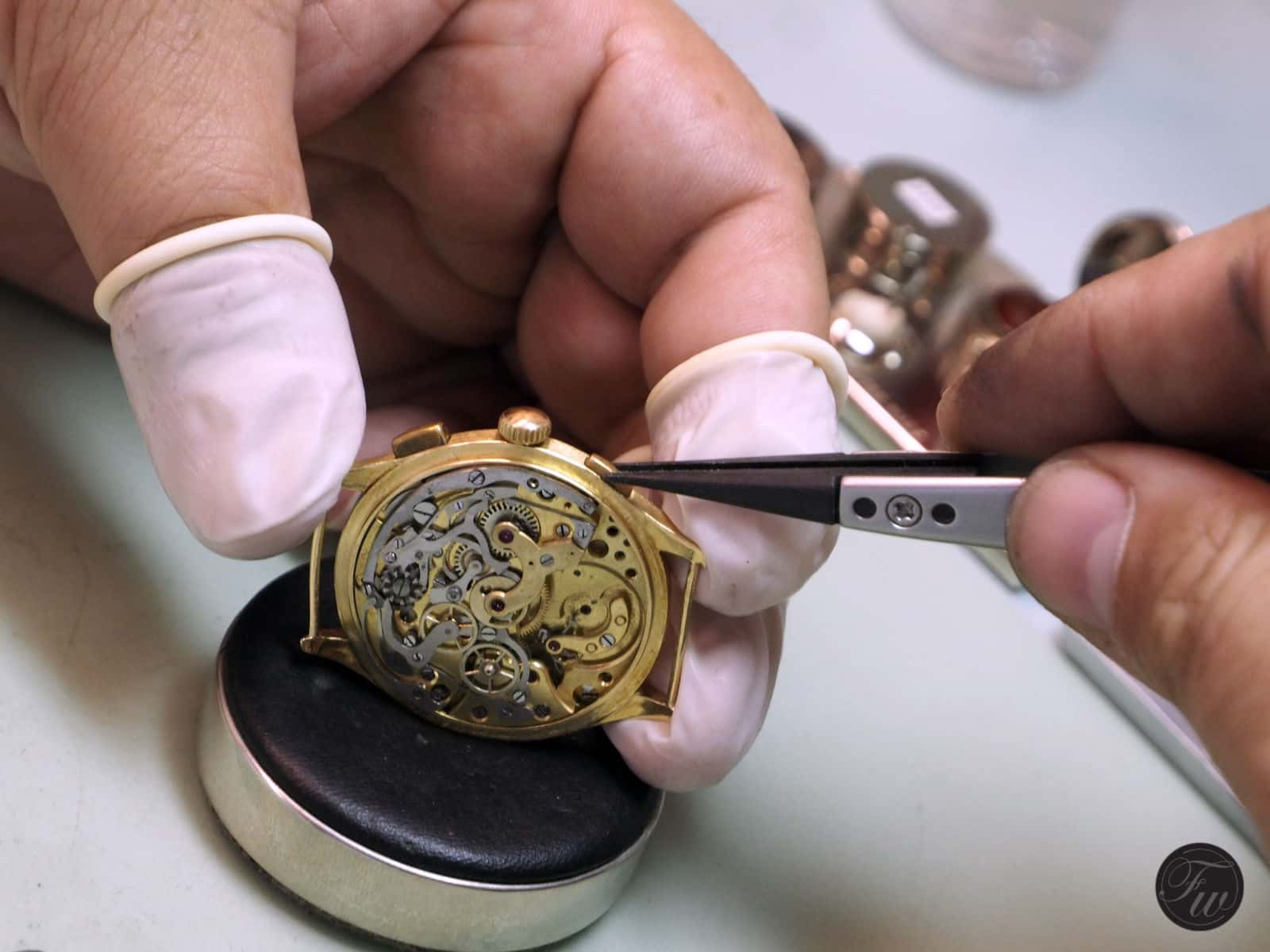
Assembling the pushers
After measuring the size of the original crystal, Kalle fits a new plexi crystal on the watch. Therefor he uses a crystal lift-tool. But only after a final inspection and removing all dust specks from the dial.
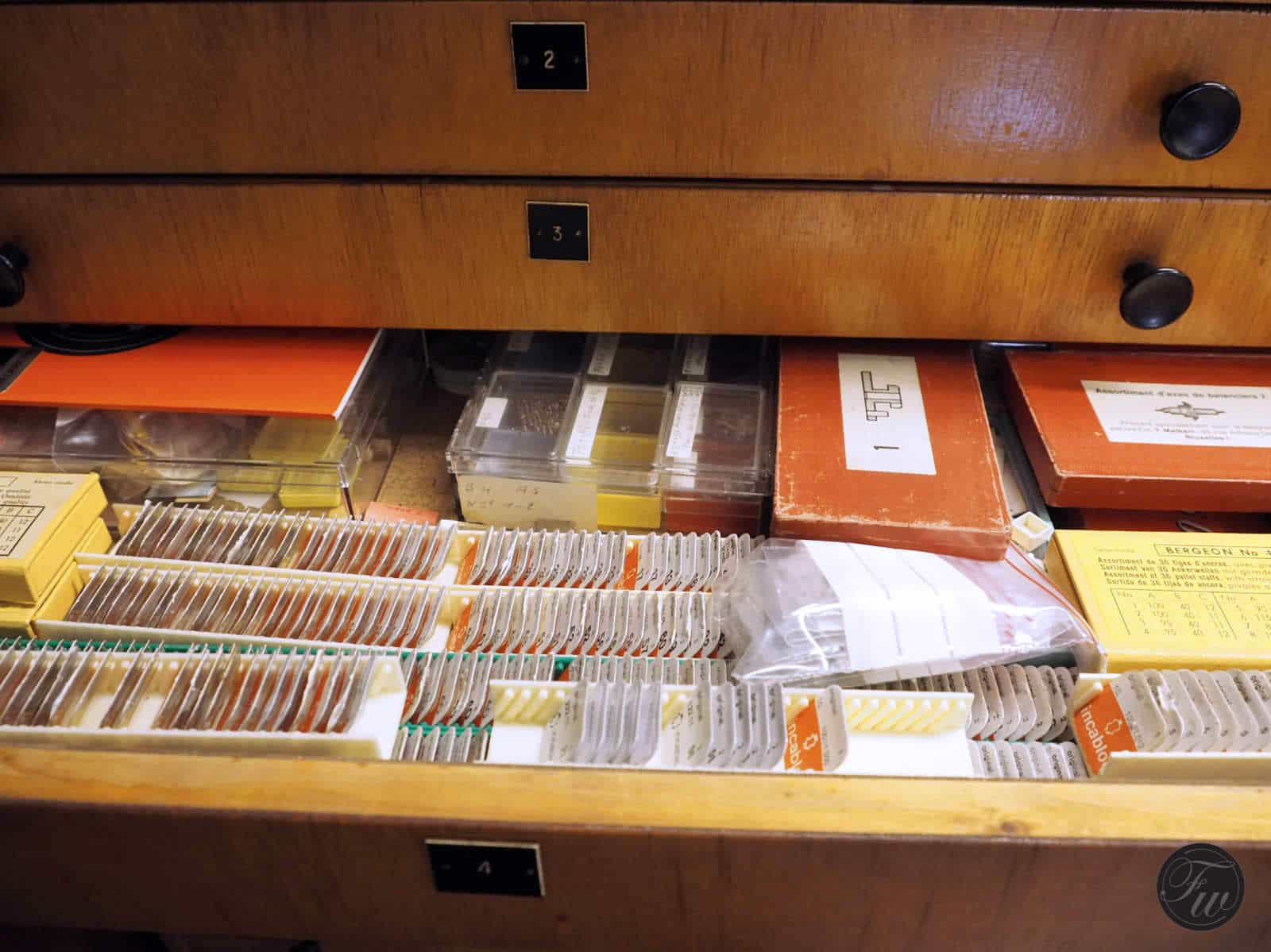
Plexi glass stock
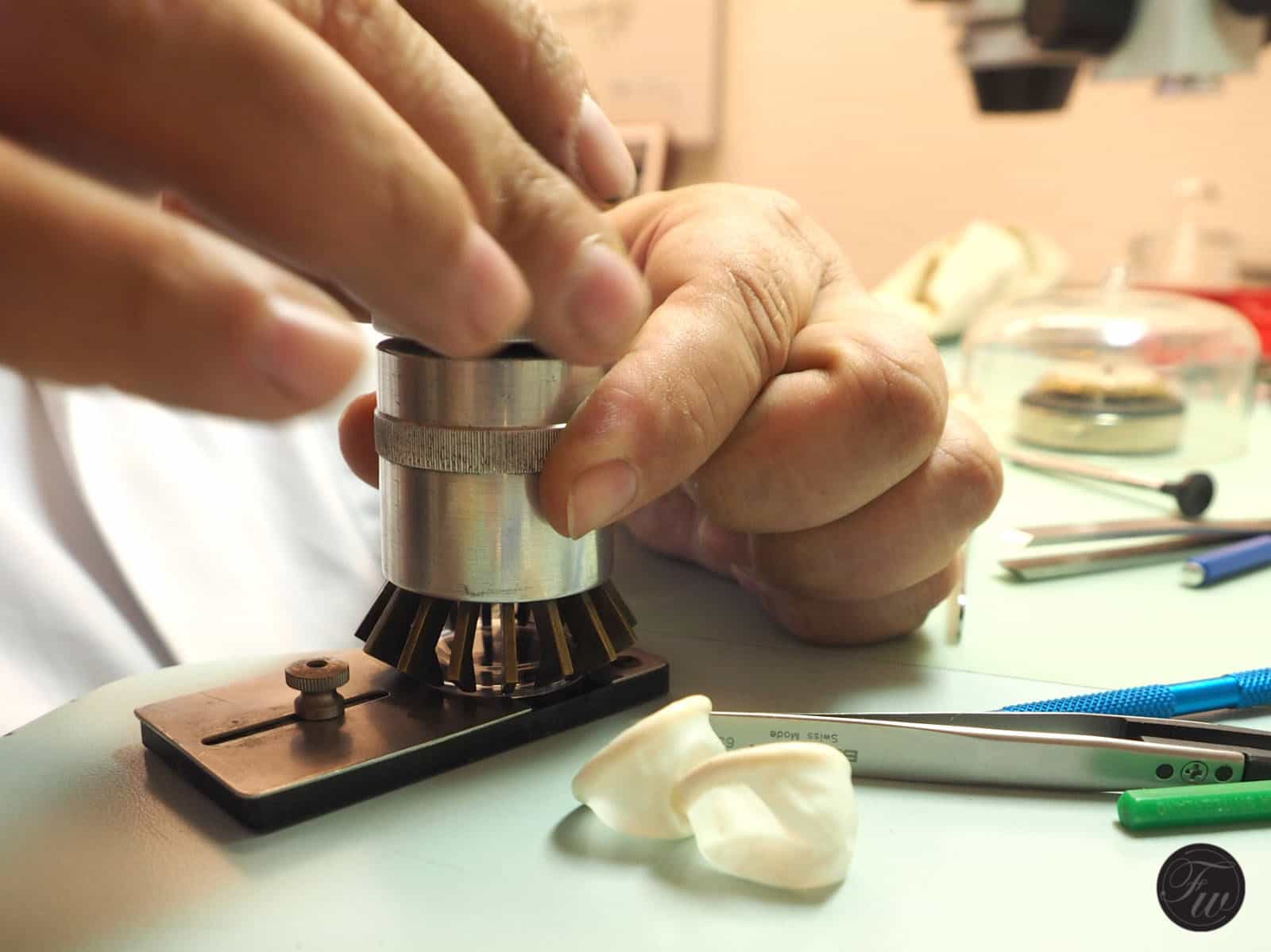
Kalle fits a new plexi glass.
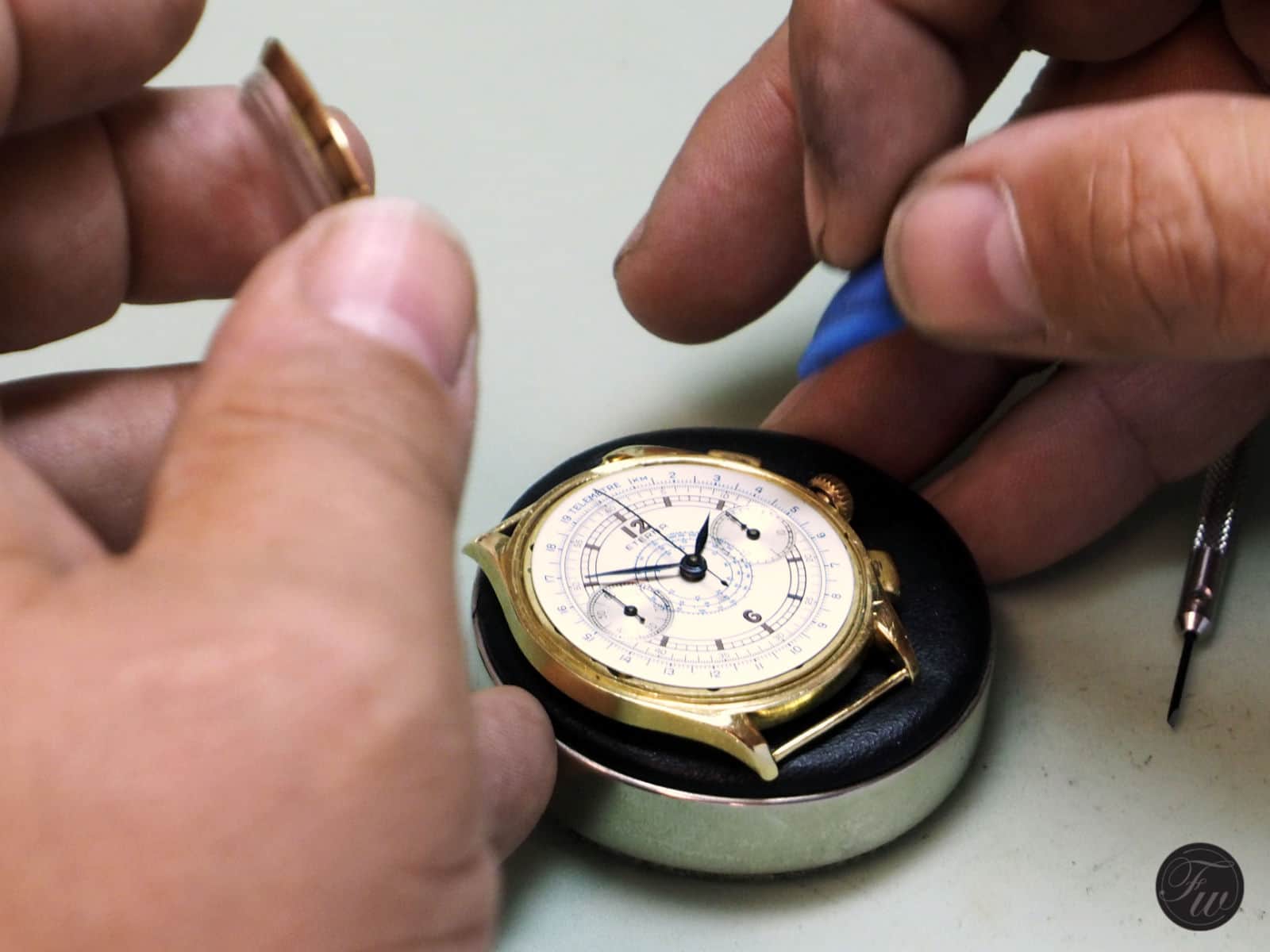
Removing the last specks

Done!
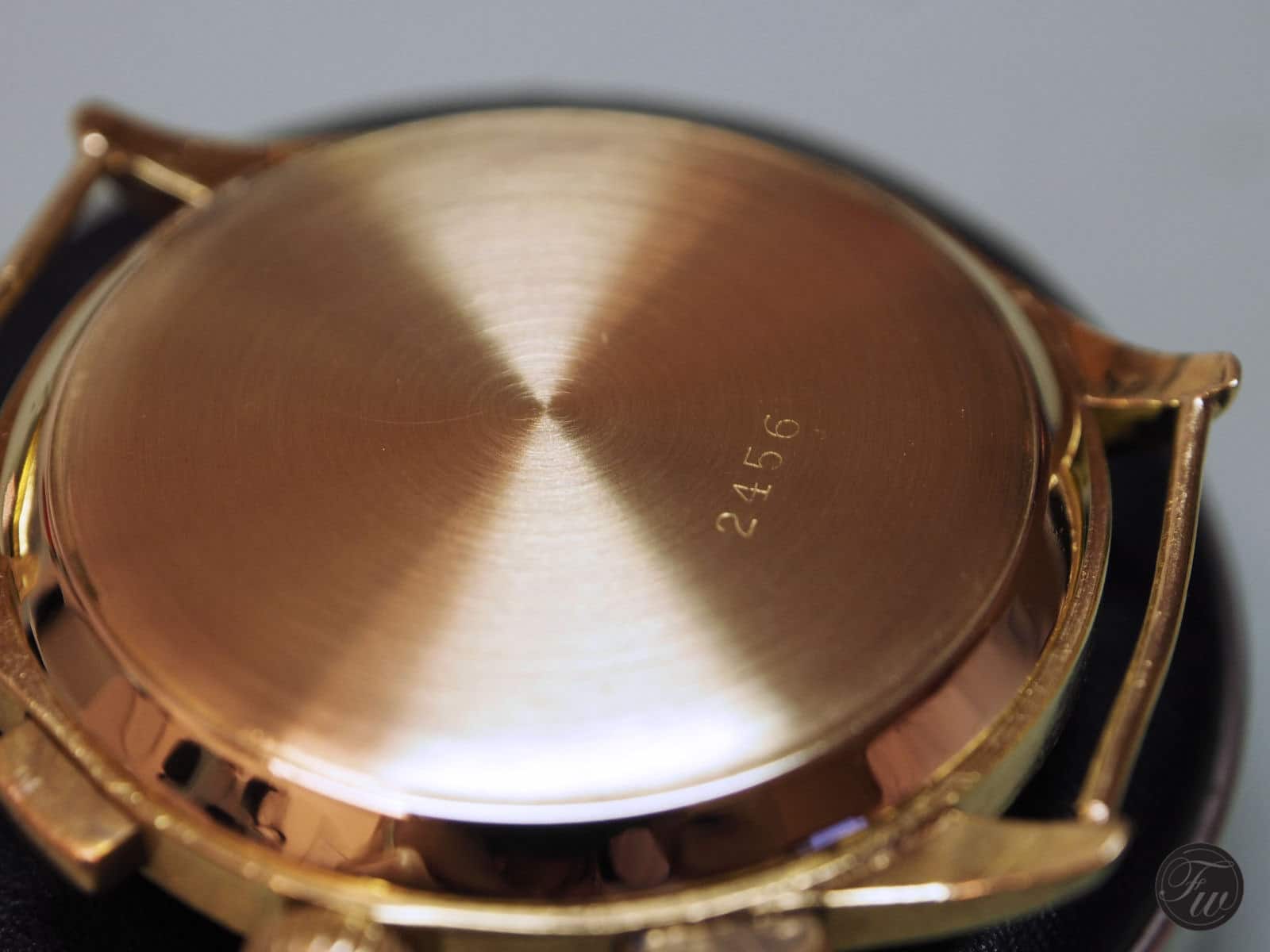
The wonderful refinished caseback
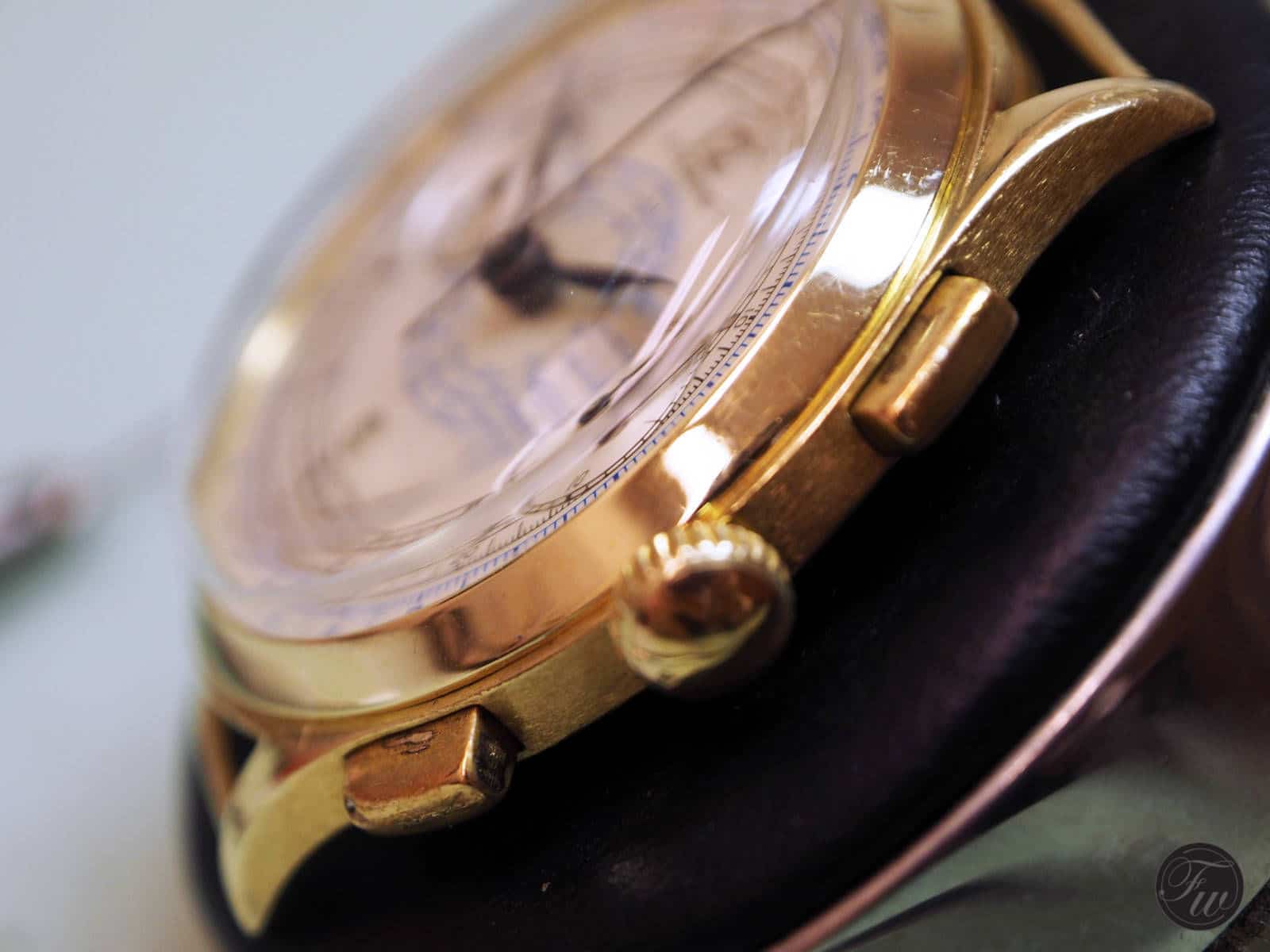
Detail of the refinished sides.
Final Words
Usually, watchmakers like Kalle don’t allow watch journalists to come this close to their work and only agree on a few generic pictures and small talk. Kalle is an exception to this rule by letting us do a full report on servicing a chronograph. I was able to take all the pictures I wanted and could ask whatever came to mind while Kalle serviced the watch. Thank you, Kalle Slaap, for your hospitality and allowing us to show your work to our readers.
For more information, visit Kalle Slaap’s website here.