Fratello Exclusive: An Inside Look At The MoonSwatch Production Facilities
On March 24th, something big happened. Together with Omega, Swatch introduced the Bioceramic MoonSwatch. Eleven different watches, each named after a different body in our solar system. From the Sun, to the (dwarf) planet Pluto, each in a different color, but all inspired by the most iconic chronograph in the world — the Speedmaster Moonwatch. To some, this introduction came as a shock. To others, it simply brought a smile to their face. Whether these were die-hard Speedmaster enthusiasts or those who had never owned an analog (or any) watch before, people jumped on them. This led to crazy moments on March 26th when the world’s 110 Swatch boutiques got their stock of MoonSwatches. And the queues are continuing to this very day.
The MoonSwatch Effect
The MoonSwatch has been one of the biggest watch releases in decades considering the attention it (also) received from mainstream media. It showed that Swatch (still) has the power to disrupt the watch industry. Whether you like the MoonSwatch or not, it has been a topic of many (heated) discussions. It also brought watches to a new audience and could be the starting point for new watch collectors and enthusiasts. The MoonSwatch even had a positive effect on the sales of the Omega Speedmaster. This is not only according to Omega’s CEO Raynald Aeschlimann, but also information that we’ve learned from independent sources. It even worked for one of Fratello’s young staff members, Sinara, who decided to purchase the Moonwatch after owning the MoonSwatch for a month or so.
Get them into Swiss watches
Even during the Watches And Wonders exhibition in Geneva a week after the MoonSwatch introduction (none of the Swatch Group brands take part in Watches And Wonders), some of the brand representatives exhibiting there seemed more interested in checking out the MoonSwatch on the wrists of our team and discussing them than in talking about their own novelties. Even there, we noticed there are two groups of people — those who like the MoonSwatch and those who don’t. Everyone, however, agreed on one thing: the MoonSwatch puts watches, especially Swiss-made watches, in the spotlight for a massive worldwide audience. As such, it’s a great chance to get them into Swiss-made watches, whether they’re luxury pieces or not.
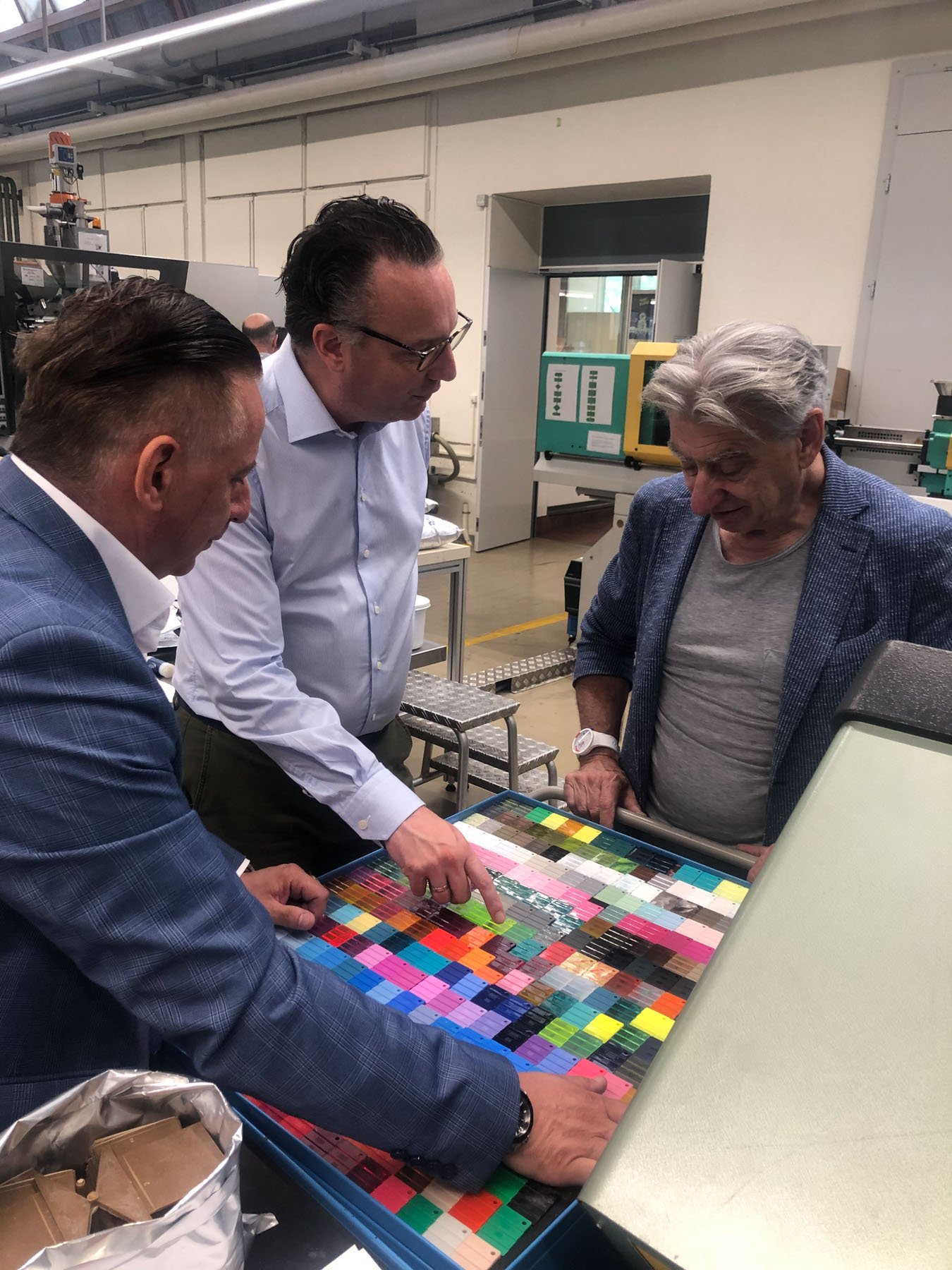
ETA CEO Mr. Casafina, myself, and Mr. Hayek Jr., CEO of Swatch, inside one of the Swatch production facilities
A visit to Swatch
I contacted Swatch Group CEO Nick Hayek Jr. to ask for a closer look at the production of the MoonSwatch. He, of course, invited me instantly. After having an informal talk with Mr. Hayek on a Thursday morning at the Swatch Group headquarters in Biel, where I was able to ask a lot of questions surrounding the MoonSwatch (we will share the questions and answers with you on Fratello at a later stage), we went to see the different production sites for the MoonSwatch watches.
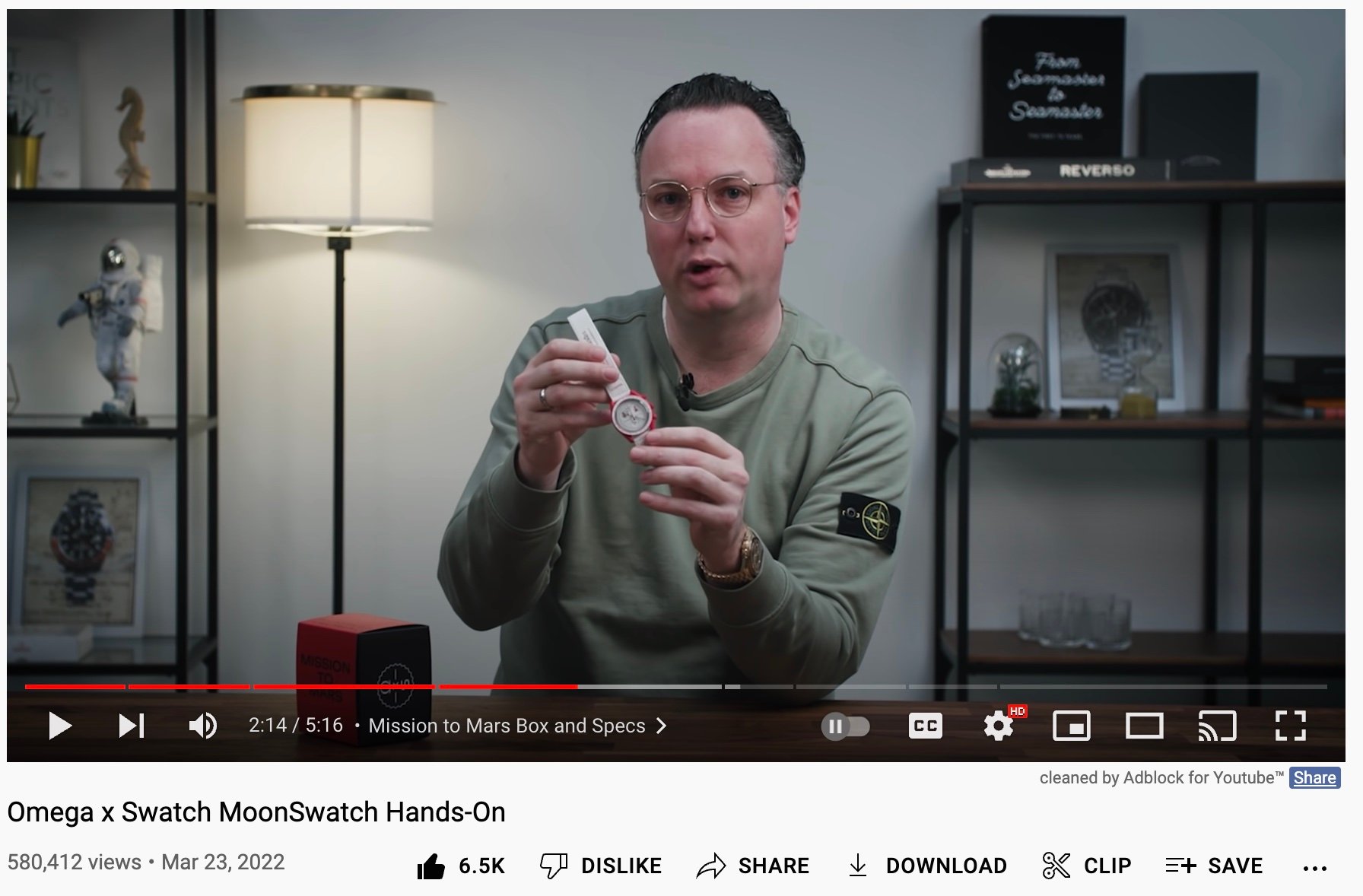
Our MoonSwatch video received over 1,300 comments and another 1,000+ via our articles and on our social media channels.
So many questions about the MoonSwatch
Let me already share with you that during this write-up, almost a week after the visit, I am still in awe of what I saw in Switzerland at the Swatch production sites. Within just this one day of visiting the sites, one could debunk so much of the MoonSwatch misinformation that’s out there. We’ve received over 2,000 comments on our channels, including this website, about the MoonSwatch. On more than a few occasions, I’ve come across the comment that these watches are made in China. This is 100% not the case. But you will see that for yourself in this article.
Visiting the MoonSwatch production sites
Together with Mr. Hayek, ETA CEO Damiano Casafina, and Omega Vice-President of Product Gregory Kissling, we started out at one of the ETA sites in Grenchen. This is where Swatch composes its Bioceramic material and where the production of the Bioceramic MoonSwatch cases, pushers, crowns, and battery covers takes place. It was surprising to see that Swatch actually produces the material itself, too. Swatch introduced Bioceramic in 2021 after releasing Swatch Bioreloaded in 2020. The Bioreloaded material was made of castor oil extracted from the seeds of the Ricinus communis plant. Bioceramic comprises mostly bio-sourced materials, ceramic powder, and color pigments.
From powder to a MoonSwatch case
At the ETA factory, we walked through a large hall with all sorts of machines injecting the material into molds. For the main case, the machines inject Bioceramic into a mold of the famous Speedmaster case. There are also robots that measure the transparency of Swatch crystals and machines that just produce the Bioceramic pushers, battery covers, and so on.
At the end of this hall, we turned left. We entered a room where a large machine was making what I can only describe as some pretty sinister sounds. Nearly at the end of this rather closed, non-revealing machine, there were long trails of Bioceramic material, gooey looking (I haven’t touched it, so it might not be that gooey) and in a bright color.
Apparently, I was witnessing the production of the Bioceramic material for the MoonSwatch Mission to Venus. I did try (or dare) to ask about the mix in the machine in front of us. Mr. Hayek, however, answered that it’s a bit like Coca-Cola’s secret recipe and, of course, patented by Swatch. Fair enough. What he did show was one of the ingredients that go into the machine — white ceramic powder.
I could not detect any type of grain or texture. It was just an incredibly smooth powder. The trails of Bioceramic material are then cooled. At the very end of the machine, you find the end result for this stage in MoonSwatch production — Bioceramic granules.
Swatch then uses these granules for all the machines that we had passed in the big hall. These machines run 24 hours a day. We walked over there, and Mr. Hayek casually let me know that he enjoys walking around this area. I can imagine him driving from his Swatch office in Biel — a very recognizable one thanks to the pirate flag outside his office window — to Grenchen on any given day of the week, any time of the day to see how the Swatches come to life or to see the new colors and designs the brand is experimenting with.
We stopped by nearly all the machines, from the ones that do the Bioceramic injections into the Speedmaster case molds to the ones that produce the battery covers. It’s interesting to know that the covers are blanks, so they don’t have any planet printings on them yet.
The Bioceramic granules are the starting point for these machines. Under a certain temperature, the material becomes fluid, and the machines can inject it in any kind of shape. Swatch also produces the MoonSwatch pushers, crowns, crystals, and bezels at this location.
Here, it began to dawn on me that this entire operation is not for only a few thousand or even tens of thousands of MoonSwatch models. It’s thousands per day!
Painting and printing at the Rubattel & Weyermann facility
It’s here where I said goodbye to Mr. Hayek, as he must have had a thousand other things to do being the CEO of the Swatch Group. I was already grateful that he joined me for all these hours so far. Our next stop was a location not far away from this ETA building and also in Grenchen. It’s called Rubattel & Weyermann, a dial maker since 1890 that has been part of Swatch Group since 2002. It is here where I witnessed how the dials are painted, stamped, and printed.
A brass band containing five attached dials is machined in order to produce the three sub-dials (with the same angle and circular pattern as the original Speedmaster Moonwatch) and the external beveled minute track which features the famous step. For the Mission to the Sun version, the machines apply the sunburst finish before the machining of the three sub-dials. After the machining, the brass band is galvanized (in order to stop corrosion) and then painted.
The MoonSwatch dials receive their layer(s) of paint and get their hour markers, numerals, and logos on them via a transferring process. Some watches, like the Mission to Saturn, also have a graphic (in this case, the Saturn planet with the ring) on the dial. An impressive piece of equipment takes care of this.
It is also here where the battery covers receive their printed planet decoration. The blank battery covers go into large trays and disappear into this industrial printer. This machine can also print other parts, such as dials and Velcro straps.
In the case of the dials, the printing of course happens after the machine stamps and paints them. As the paint color needs to match the Bioceramic color, Swatch prepares its own paint mixture in a separate department. Then, there’s a quality-control check before the painted and printed parts leave the Rubattel & Weyermann premises.
Technicians perform this check, visually inspecting all parts for discrepancies. At this point, I started to wonder how it was possible that the MoonSwatch has a price tag of only €250. Swatch developed and customized machines specifically for the MoonSwatch production. Not only that, there are quite a few human tasks/interventions involved during the processes that I had seen thus far. In the end, it must be about huge numbers.
The production of hands at Universo
The last stop for the day is a bit further away from Grenchen and Biel. We were heading to La Chaux-de-Fonds. This is a name that might sound familiar to you, as it’s the home of many watch manufacturers and suppliers. One of those suppliers is Universo, which the Swatch Group owns. Universo not only produces hands for the Swatch Group brands but also for a few other well-known watch manufacturers. It is here where the company produces hands from FlikFlak and Swatch to Breguet, each to their own standards, of course.
During this visit, I could see the production of the MoonSwatch hands from start to finish, and it was an impressive journey. It all starts with a long brass strip that is spray painted in a special cabin with the appropriate color for the MoonSwatch model. When I was there, Universo was doing this for the Mission to Mars in all red. The long brass strip stays on a spindle with a protective layer for the paint and goes into an industrial oven. After this, the red painted metal strip gets transferred to a large hall with all sorts of machinery. One machine punches the holes in the strip so that the hands can be mounted correctly to the watch in a later stage, as well as punching a hole where the pinion needs to go. Afterward, a canon is placed in the pinion hole and checked to ensure that the hole is still perfectly round.
Then, the shape of the hand gets cut out from the strip. This includes the cut-out for where the Super-LumiNova will go. The hands remain attached to the long brass strip though. The hands then go to the machine that applies the lume to the backside of the hand, and thus, the strip. After this application, a layer of lacquer is added to the Super-LumiNova to get exactly the right color. It’s the exact same color you will also find on the stepped sub-dials and the minute track on the outer dial. Swatch takes details incredibly seriously. In the final stage, technicians optically check if all the hands in the strip are still straight. Most importantly, they also make sure there are no visual flaws on the finished hands.
The MoonSwatch hands are now ready to go to their next stop, but my trip to the MoonSwatch production sites ended here. Next time, I will see some of the other production sites (there are five in total for Swatch). In the video below, you will find some footage of the production of the hands as well as other parts.
Let there be no misunderstanding: the MoonSwatch is Swiss-made
On the way back to the airport, I had to digest what I’d seen during the day. Now, even more than before, I am convinced that the introduction of the MoonSwatch was a genius move by Swatch and Omega.
What surprised me most was the level of detail provided by the MoonSwatch and how much effort Swatch puts into getting it right, also quality-wise. And yes, this watch is all Swiss-made. Let there be absolutely no doubt about that.
More of our articles on Swatch can be found here. Let us know if you enjoyed this exclusive look behind the scenes in the comments!